Known as a vital bulk commodity throughout the industry, fertilisers must be handled carefully in order to minimise the level of product degradation and dust generation during loading procedures. Without a safe, reliable and efficient loading system in place, dry bulk fertiliser loading can have a negative impact on the environment.
The Cleveland Cascade Ltd loading system utilises a series of inclined cones to direct material flow and reduce the velocity and impact of the material. A state of “mass flow” is achieved allowing the material to move as a single mass throughout the system to form stockpiles at the outlet reducing the effects of segregation. Dust generation is practically fully negated through the use of the Cascade system eliminating the need for expensive, high maintenance dust extraction and filtration systems.
Many systems have been supplied for the loading of fertilisers by Cleveland Cascades across Europe, Africa, Asia and North & South America. Some examples of these are discussed below:
CC850
A Cascade Ship loader was supplied for loading fertilisers at rates of up to 2,100 metric tonnes per hour to the Port of Aqaba located in Jordan. A pivoting head chute is featured to allow for the system to remain level as the luffing boom of the ship loader manoeuvres to load between operating angles of -2° to +11°.
In a fully extended state the system can reach 20.0m long from the interface to the outlet, a retracted operational length of 7.7m can be achieved which is measured to the base of the skirted outlet. This system was provided with a head chute maintenance platform allowing routine inspections to take place alongside observations for material behaviour during loading.
Given the loading rates and the density of the product it was apparent from the inception of the project that a large sized cone would be required. The required volumetric rate for this project was calculated to be 2,211m3/hr, this meant that the Cleveland Cascades Ltd 1700 GRP profiled rim cones were required. The selected cones have a maximum capacity of 2,800m3/hr surpassing the customers’ requirements and allowing for any material surges.
Liner selection was of utmost importance as various materials would be loaded through the system, it was decided that UHMW PE would serve as the best choice due to its low co-efficient of friction reducing the ability of the material to ‘cake’ and stick to the liner. Because of this, an anti-static path had to be provided and was achieved by using stainless steel banding between each of the cones and then attaching these to the head chute and carrier steel fabrications.
A unique aspect for this system was the ability to store the retracted system underneath the boom through the use of a stowing winch. This meant that when not in use the whole system could retract as the luffing boom was raised effectively occupying less area around the port.
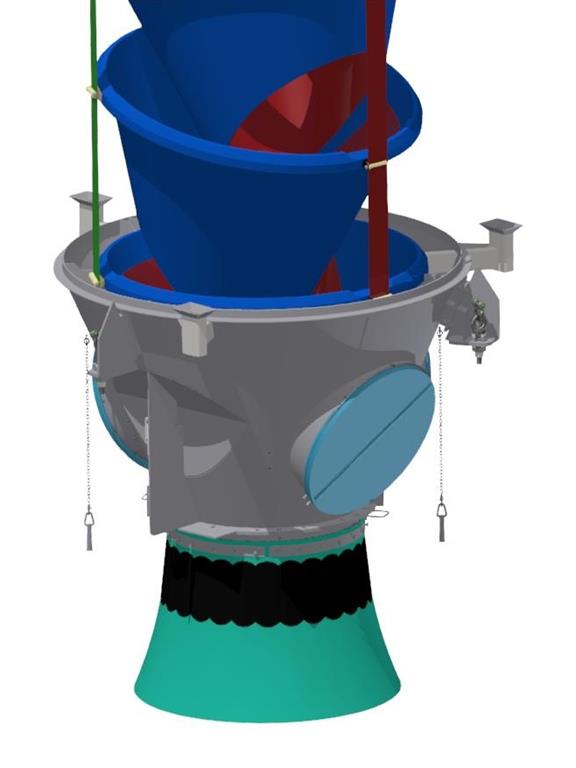 CC850 carrier with skirt
|
CC850
|
|
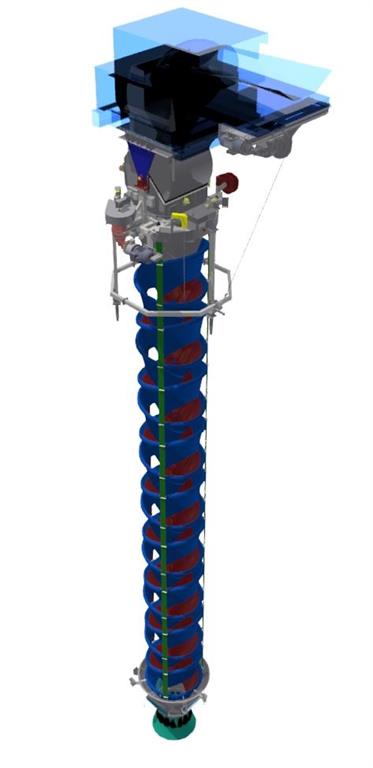
CC850.
|
CC900
This project is a Cascade Storage Loader for indoor application to be used for the loading of polyhalite and was supplied in 2018 to Loftus, UK. When fully extended the system reaches a length of 15.0m and can achieve a retracted length of 4.5m whilst still remaining operational.
For this system, the cone size required were the Cleveland Cascades Ltd 600 GRP profiled rim cones. These are one of the smallest cones produced and given the system length careful consideration was necessary with regards to cone stacking and oscillation during operation. Ceramic tile lining is applied to the cones to provide a long lasting wear resistant liner without impeding the flow characteristics of the material. These cones have a maximum volumetric throughput capacity rated at 246m3/hr which was ideal for the setup given the requirements provided by the customer. The low 80tph feed rate complimented the small cones allowing them to fill to the correct level without over spilling occurring.
At the outlet of the system a heavy rubber skirt is in place. The system is set up to automatically raise as the polyhalite comes in to contact with the material detection probes whilst still maintaining contact between the material pile and skirted outlet. This further aids with preventing dust from escaping outside of the system and into the surrounding environment.
CC900 head chute.
CC900 carrier.
CC943-6
Four identical systems have been supplied to Vistino, Russia for the use of loading fertilisers. Each system is attached to an independent ship loader via a fixed head chute design. They can achieve and extended length of 31.0 meters whilst having the capability to retract to as short as 6.6m.
Varying liners are used throughout the system, within the head chute stainless steel is featured for corrosion protection and to provide extra wear resistance as material enters the system from the conveyor belt. The cone selection for this project were the Cleveland Cascades Ltd 1700 GRP profiled rim cones which feature UHMW PE liners, this is apparent for the trimmer also and provides ample abrasion protection as the material is brought under control as it travels through the cascade.
Both a skirt and interchangeable trimming spout are supplied for each system. This allows for conventional loading to take place forming material stockpiles using the skirted outlet. Following this, any void space within a vessels hatch can be utilised through using the trimmer outlet by providing material throw in a controlled manner to occupy the available area.
The telescopic system is operated by a remote drum winch and features a complete suite of electrical components for system safety and automation.
CC943 Carrier trimmer. CC943 Chute.
CC943 Head Chute. CC943 Outlet