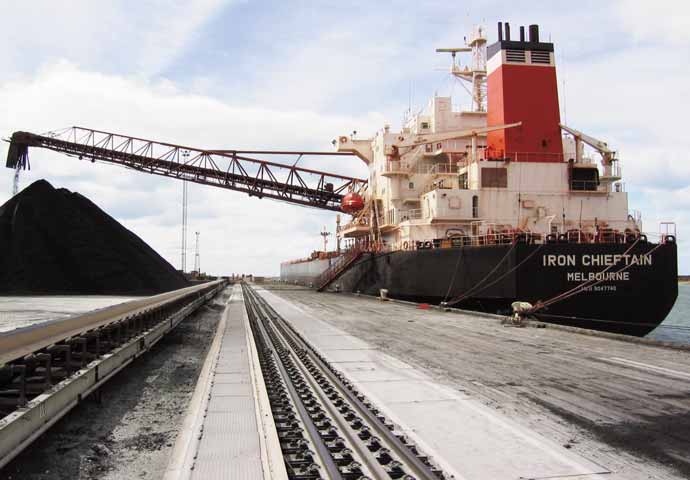
Another pearl in the ocean for Coeclerici
The Floating Transfer Station Bulk Sumatra, in July 2013, in line with the delivery schedule, is the fourth unit to join the Coeclerici fleet currently operating for PT Berau Coal in East Kalimantan in Indonesia, writes Capt. Giordano Scotto d’Aniello, Head of Commercial Department, Coeclerici logistics division, Milan, Italy.
CUSTOM DESIGNED FOR GREATER EFFICIENCY
During the last few years, Coeclerici has expanded into the Indonesian market significantly through the use of the Floating Transfer Stations (FTS), contributing consistently to its clients’ ever-growing trading activities.
Coeclerici units, for PT Beau Coal, were designed to the specific need of the client right from the drawing board, and it proved to be the perfect solution for the client when it became apparent that more offshore transshippers would be required as a result of their expansion in the coal production market.
BULK SUMATRA MAIN CHARACTERISTICS The FTS is a 11,855dwt unit fitted with two Liebherr heavy duty cranes with grabs, two hoppers, a belt conveyor system and two swivelling shiploaders to discharge simultaneously into ocean going vessel (OGV) cargo holds; the system is designed to reach a peak loading rate of 2,400tph (tonnes per hour).
The shiploaders have an outreach of 30m and have been designed to have an adequate slewing range by which, together with the rotating chute installed at the end of the FTS loader, they are able to reach all the spaces of the cargo hold that need to be loaded and thus guarantee efficient loading of the OGV up to Capesize.
The luffing range of the shiploaders +6° (up) and –15° (down) allow the discharging chute to keep very close to the hatch cover in order to avoid any cargo spillage. This, together with the installation of even more efficient scrapers on each conveyor belt, is part of a host of technical solutions adopted to be as environmentally friendly as possible.
The shiploader’s steel structure has been designed, constructed and certified by RINA to be capable of lifting a load of 10 tonnes at 21m outreach, allowing the transfer of a payloader for trimming purposes onto the OGV without changing the mooring position.The conveyor system is equipped with an SGS sampling system, metal detectors and weighing scale for a non-stop checking of the coal operations.
The ‘conveyor control cabin’ has been intentionally placed on the highest point of the unit to ensure the continuous control of the loading operation cycle; five cameras have also been placed in strategic positions to always assure the best efficiency and safety of the entire system.
The mooring equipment has been duly fitted on board to make it suitable for the coal barges working in the area, while the accommodation on board has been designed to host external personnel, like dozer operators, service engineers and sampling professionals.
CYCLE OPERATIONS
According to the loading schedule plan already agreed between the FTS terminal manager and the OGV Master, upon OGV readiness the first step is to establish the communication between the FTS and the OGV Captains by planning the positioning of the shiploaders. The transshipment operations start from the moment that the FTS is safely moored with its port side to the OGV and the feeder barge, transporting about 6/8,000 metric tonnes of coal, is safely moored on the starboard side of the FTS.
The two cranes grab the cargo from the barge that feed the conveyors system via the two hoppers of about 50m3 strategically positioned to maximize the cranes’cycle. Thespecificoperatorsmakesurethat the conveyors are working in compliance with the system parameters while other crew members check that all the operations are running smoothly. All the operations can easily and precisely be checked through the panel installed in the control cabin, which is fitted with all the regulators and alarms.
During the Bulk Sumatra commissioning phase, Coeclerici’s technical staff, in close collaboration with the Captain and crew, PT Berau Coal technicians, as well as the equipment service engineers, verified that all the facilities involved in the operations and the communication between the actual performance and the project specifications were always complied with.
EXCELLENT PERFORMANCE OPERATIONS
The Bulk Sumatra’s latest delivery has marked another important step on the high technology offshore transhipment solutions Coeclerici provides to its client. The unit, during the commissioning period, showed an outstanding performance with a rate of 52,028 metric tonnes per day, thanks to Coeclerici’s dedicated technical team that, together with Coeclerici’s trusted suppliers, has been able to develop a combination of reinforced, powerful & reliable equipment fitted on board of the unit.
The existing Coeclerici fleet working for PT Bearu Coal, the fifth-largest Indonesian producer, has already handled 16mt (million tonnes), since the first delivery of the first FTS Bulk Java in July 2011.
If we consider that the second FTS Bulk Borneo was delivered on July 2012 and the third one, Bulk Celebes, on January 2013, the fleet, with the delivery of Bulk Sumatra, presently are exporting about 1.5mt per month with a potential throughput of about 3mt per month.
In the next few years, the figures will become remarkable if we include the quantity that Coeclerici’s fifth FTS, Bulk Pioneer, has been handling in Indonesia for KPC since 2003, which, in 2012 alone was 6.5mt.
The above figures show the huge achievement of the Coeclerici logistics division in Kalimantan, which in the coming years will have the potential to handle a good 20–25% of all the coal moved offshore in Indonesia.
CONCLUSION
The various satisfied customers accross the globe are testimony to the importance of all Coeclerici’s working units.
In keeping with the company’s strategy, Coeclerici will continue to explore new market areas, which will no doubt result in another string of newly pleased customers all over the waters of the world.
Innovation-driven CSL celebrates 100 years of coal handling solutions
As CSL celebrates its 100th anniversary this year, the world’s largest owner and operator of self-unloading vessels continues to drive innovation and create efficiencies for coal customers worldwide.
In Canada and the Americas, CSL’s latest-generation Trillium Class Laker and Panamax self unloading newbuilds have been operating along the continental coasts since late 2012. Featuring the most advanced self unloading technology available today and IMO Tier II engines, the Trillium-class ships use less fuel, release significantly fewer emissions, minimize cargo residue and provide superior operational efficiency for coal trades.
As part of CSL’s ambitious fleet renewal program, the three new Trillium Class Panamax ships and four new Lakers will be joined by two new bulk carriers in 2014.
COAL TOP OFFS IN THE AMERICAS Along the East Coast of the United States and in the Gulf of Mexico, CSL Americas has been performing offshore coal top off operations whereby a CSL Panamax self-unloader transfers coal into a lightloaded Cape. This operation ensures the Cape vessel is fully loaded before it departs North American waters for export markets, producing higher revenues for cargo owners. With permits and procedures in place on the West Coast of North America, CSL is ready to perform similar operations in the Vancouver area.
MOVING COAL VIA CANADA’S NORTHERN CORRIDOR
Canada’s Northern Corridor has become an efficient channel to move low-sulphur thermal coal from the Powder River Basin in the Western US to end-markets in Europe. Using high-capacity self unloading Lakers, Canada Steamship Lines loads coal in Superior,Wisconsin, which is then discharged in Quebec City and reloaded to ocean-going vessels bound for European markets.
INTEGRAL ROLE OF SELF UNLOADERS IN AUSTRALIAN COAL SUPPLY CHAIN In Australia, the Iron Chieftain is an Australian shipping stalwart – a 50,587dwt self unloading vessel that has been delivering coal from East Coast Australia to South Australia for the last 20 years. With hoppered holds, gravity fed gates and a C-loop belt, the Iron Chieftain has been reliable and consistent throughout the years — carrying over 900,000 metric tonnes of coal and 1,000,000 metric tonnes of iron ore per annum.
With experience loading at all major Australian coal ports, the Iron Chieftain provides fast and environmentally-friendly self- discharging and has become integral to the success of the customer’s supply chain.
The 72 metre boom and self unloading system can achieve a maximum discharge rate of 2,500tph (tonnes per hour) and an average unrestricted discharge rate of 1,500tph.The shore-side operation at Whyalla allows for unrestricted discharge directly on to the coal stockpile, thus requiring minimal shore infrastructure and investment. The speed, efficiency and cost effectiveness of the Iron Chieftain discharging operation is highly valued by the coal receivers.
MEETING CUSTOMERS’ HIGH STANDARDS IN EUROPE CSL’s youngest division, CSL Europe, understands that coal customers in European coastal markets seek a balance between economies of scale and a tailored approach that meets their specifications. While markets remain difficult in Europe, CSL believes the next few years will bring a period of change and renewal to the European bulk shipping market, resulting in higher customer standards in the areas of fuel efficiency, environmental and operational performance, and cost-competitiveness.With its diversified fleet, rapid unloading rates, dust-free discharge booms, and reduced infrastructure requirements, CSL Europe is well equipped to respond to these demands and deliver superior operational efficiencies.
MacGregor systems provide flexible cement handling for new Japanese cement carrier
A new self-loading/unloading cement carrier for Japanese Taiheiyo Engineering Co will feature MacGregor cement handling systems designed to carry three grades of cement at a rated capacity of 1,000 tonnes per hour.
MacGregor, part of Cargotec, has secured a new order for autonomous loading and unloading systems for an 8,700dwt cement carrier to be built for Japanese shipowner Taiheiyo Kisen Kaisha Ltd.
“The totally enclosed cement handling arrangements will ensure flexible, efficient and clean cargo operations,” says Anders Berencsy, Sales Manager, Selfunloaders at MacGregor. “An additional benefit is that the computer-controlled systems are programmed for automatic operation by just one person.”
The 109m vessel will have four cargo holds, each divided into two compartments. The cement handling system is designed to carry up to three grades of cement in each shipment.
During loading operations, the ship’s deck-mounted receiving aeroslide is connected to the shore facilities by flexible bellows; loading can be achieved on either side of the vessel.
The cement is then transferred to two short intermediate aeroslides by means of hydraulically-actuated flow control gates. These transfer the cargo to two reversible horizontal screw conveyors. One moves the cement forward to holds 1 and 2; the other serves holds 3 and 4. A combination of hydraulically- actuated sliding gates, flexible connections, hydraulically-actuated flow dividers and transfer aeroslides complete the delivery of the cement to the selected drop off points. Maximum level guards indicate when the holds are full, while pneumatically- operated shut-off valves avoid contamination between different grades of cement. Sloping aeration panels installed on the tanktop of each hold are the first elements in the discharge system. Air blown through the panels fluidizes the cement, allowing it to flow towards the centre of the hold, where it feeds into a vertical screw conveyor equipped with two remote-controlled flow control gates.
At deck level the cement returns to the reversible horizontal screw conveyors and is conveyed to a buffer hopper inside the pump room, located amidships. From the hopper the blow pump system transfers the cement to a silo ashore via two pipes. Dust collectors are installed on deck.
MacGregor is a leading brand of engineering solutions and services for handling marine cargoes and offshore loads. MacGregor products serve the maritime transportation, offshore and naval logistics markets, in ports and terminals as well as on board ships. Its cargo flow solutions integrate cargo access, stowage, care and handling functions to suit a particular ship’s cargo profile. This benefits its productivity, environmental impact and profitable service lifetime.
MacGregor is part of Cargotec. Cargotec’s sales totalled €3.3 billion in 2012 and it employs approximately 10,000 people. Cargotec’s class B shares are quoted on NASDAQ OMX Helsinki under symbol CGCBV.