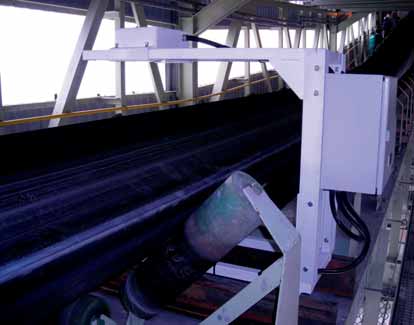
Measuring conveyed flows continuously, and using minute-by-minute results to make real- time changes can improve many aspects of a plant’s operation. Any processing operation using ore or concentrates as a feedstock needs to measure in order to control. Improved process control can provide major benefits such as: processing less waste, producing more consistent quality product, maximizing metal recoveries, generating less tailings and improving productivity. Each of these benefits individually can amount to millions of dollars per year in savings, and being able to perform better reconciliations and metal accounting is just a bonus.
Process plant performance in the coal, cement and minerals sectors has been significantly improved through the application of real time, full stream, non contact, multi-element analysers. Particle size and belt speed don’t affect the analysis. Grade control need not stop at the haul truck. Analysers on conveyors at the mine (after the crusher) are used to divert increments of undesirable material, be it waste, low grade ore, or high deleterious content so it does not enter the process plant. There are myriad savings in grinding costs, power, reagents, etc. Benefits really add up when that waste is replaced by good ore and the plant output increases for the same throughput. Ore of product quality, eg. in iron ore plants, is diverted to bypass the beneficiation plant.
Scantech is a major manufacturer of on-belt analysers for conveyed bulk materials. One of its customers consistently achieves over US $6 million per year in beneficiation cost savings alone by doing this but also maximizes plant capacity by only processing what needs to be upgraded.
Analysers help plants blend ores to ensure consistent ore feed. Reducing ore quality variability can increase metal recoveries by up to 15% in copper operations. Another customer blends copper ores to maximize leach circuit capacity and achieved a payback of less than two months. The customer now uses elements that weren’t initially of interest (Fe and S) to control the mineralogy blend as well as copper content to further benefit its process. Analysers can be used on conveyors throughout the plant.
Beneficiation circuit feed and product streams, eg on jigs, ensure optimal recovery. Analysers help optimize additive control in cement plants and adjust metal concentrate chemistry pre- smelting or sinter basicity. Measurement of product flows to stockpiles and load out flows to the train or ship are used to determine real-time stock levels (tonnes and grade) and indicate shipment quality compliance with product specification requirements. Where necessary, products can be blended or bulk sorted to improve shipment quality for each customer.
The combination of accurate, continuous microwave moisture measurements with elemental data allows dry weight percent of each element to be reported in real time. Real-time analysis allows mines to optimize processing operations. Detailed studies continue to be undertaken to help processing operations identify further improvement opportunities, eg. ore hardness through silica measurement to control grinding circuit feed rate and ore blend.
Scantech’s core business is the development, supply and support of on-belt analyzers for the resources sector, world-wide. Scantech first supplied this technology to the coal sector in the early 1980s and has now developed analyzers for the cement, minerals, power and steel sectors. More than 1,000 analysers designed and built in Australia have been sold in 55 countries. Customer service and product support is enhanced through remote access capabilities for all current models and experienced staff located in major regional locations. As a specialized supplier Scantech is able to customize analyser solutions, including application specific calibrations and support programmes including site training and radiation services.
Scantech’s units are used for conveyed bulk materials, particularly in the minerals sector with applications and years of proven operational performance in a wide range of commodities such as iron ore, manganese, copper, zinc-lead and phosphate rock.