Regulations on fugitive dust emissions in Brazil can be strict, particularly in high traffic or densely populated areas, eventually yielding fines and potential downtime if not properly addressed, writes Rodrigo Trevenzolli, Engineering Manager / Martin Engineering Brazil. Although common fugitive dust particles from dry cargo such as coal and limestone can lead to respiratory issues, grain dust emissions possess allergenic properties over and above the common air quality concerns, potentially causing further irritation.
To prevent impacting the local community and adjacent docks with dust caused by the transfer of agricultural commodities, T-Gra~o Cargo, located at the Port of Santos in São Paulo, Brazil, sought solutions to help them mitigate the issue. “We have a complicated geographic position, because we are between a passenger terminal to the north and the Brazilian Navy to the south, and across the street from the port authority,” explained Vinicius Pina, Operations Director for T-Gra~o.
Port and terminal
The Port of Santos is the busiest port in Latin America, spanning approximately eight square kilometres (three square miles). With nearly 1,500 people working in the port on a daily basis and 1.1 million passengers boarding and disembarking ships annually, the area is always bustling, so authorities monitor air quality closely to ensure safety.
Operating since 1998 at Terminal 26 on the Northern end of the quay closest to the passenger terminal, T-Gra~o manages the import and export of over four million short tons (3.6mt [million metric tonnes]) a year of malt, wheat, soy and maize. Unloading vessels using two industrial vacuum units with an offload capacity of 330stph (short tons per hour) (300tph — metric tonnes per hour) each and a loading capacity of 1,433stph (1,300tph), the company manages 42 concrete silos and eight massive metal silos, totalling 126,000 short tons (114,000 metric tonnes) of storage capacity.
Spanning only 150,000ft2 (14,000m2) of dock space, the company is considered one of the smallest grain terminals in Brazil, but processes more grain per square metre than larger competitors, making it the most efficient operation of its kind in the country. Offering customs clearance, cargo delivery and reception, logistics and warehousing services, T-Gra~o serves a variety of customers from international importers to farmers across the State of São Paulo.
“As our production has increased over the years, so have fugitive dust emissions,” said Pina. “We’ve worked closely with regulators and neighbours to address air quality issues.”
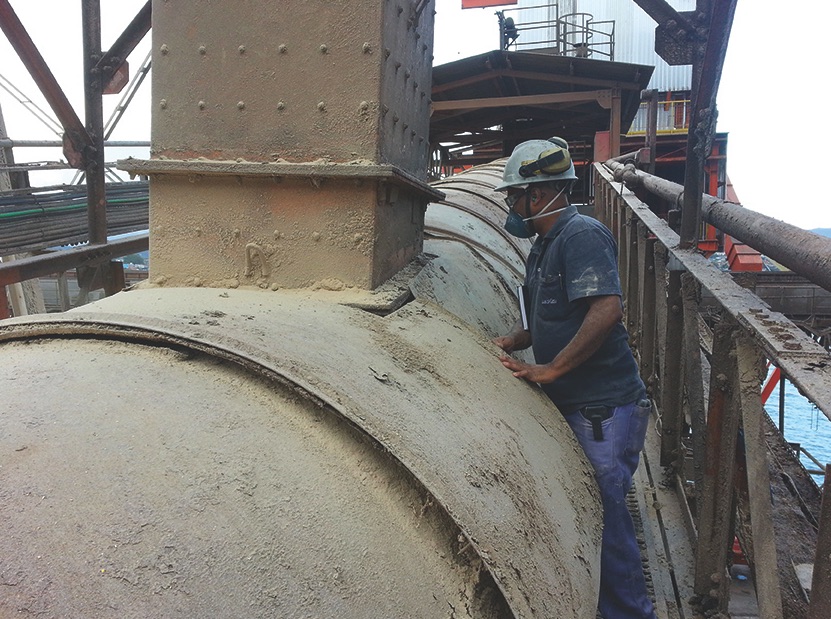
Wearing a protective mask, a worker inspects the outer transfer chute.
Particles and people
Environmental controls are important in grain transport to not only prevent dust from escaping, but also to protect against excess moisture, which can lead to mould growth. Receiving cargo from trucks in an enclosed area, the material is quickly carried on covered conveyors to the proper silo to be stored for eventual loading and export.
The biological purpose of grain pollen is to travel long distances on atmospheric air currents, but processing adds light dried material, which significantly increases the volume of emissions during industrial handling. According to a study by the University of Wisconsin conducted on grain particulate emissions at harvest time, breathing in grain dust impacts the health of producers as well as others who work in the industry.[1] Low levels of exposure can cause chest tightness, sore throat, nasal and eye irritation. Long term exposure can produce ongoing congestion, and can be a significant problem for those with asthma.
Transfer points at T-Gra~o range between 32-50 feet (10-15 m) in height. As dry organic material was dropped from one belt to the next, the impact created turbulent air pressure that forced dust out of openings in the chute. The fugitive emissions significantly lowered air quality and visibility in the immediate work areas, forcing workers to wear protective masks when working around any part of the conveyer system. The dust often travelled beyond the site line.
The Santos Estuary — the waterway that serves the port — is partially protected from high winds off the Atlantic by a wind shadow created by high-rise buildings and hilly terrain along the coast. The placement of Terminal 26 in the northern part of the port, however, leaves it exposed to wind travelling up the estuary. Depending on the direction and force of the wind, dust created at the transfer points had the potential of travelling long distances.
“Complaints were fairly common, and our proximity to the port authority allowed an immediate response from inspectors,” Pina said. “When we received a complaint, we acted to address the issue right away, but we needed a long-term solution.”
Dust and fines piled along the belt path, fouling rolling components.
Battling dust
Utilizing a cleaning crew of 45 workers for 24 hours per month, the inner and outer areas were thoroughly cleaned. However, according to managers, grain particulates must be cleaned and deposited correctly. “Investment in cleaning equipment just to control dust buildup was high,” Pina explained. “Along with using brooms and other basic equipment, we purchased an expensive Italian-made sweeper. Cleaning occupies labor from other operations, spans large areas of the dock and warehouse, and ends up creating dust while it’s being done.”
Operators first sought an answer to the dust by bringing in an equipment manufacturer that installed a transfer chute. This was intended to contain dust from the discharge flow as it fell onto the belt. What it did not do was control emissions at the loading zone where the impact would cause plumes of dust to escape. The dust filtration system attached to the settling zone chute was inadequate, due to the volume of emissions and a poor chute design.
“In any given week, the dust system required maintenance one day and broke altogether the next,” said Pina. “At one point, a breakdown caught us unprepared at a critical moment and resulted in costly unscheduled downtime.”
Rethinking the transfer point
With complaints still periodically coming in from neighbours and ongoing internal air quality issues, T-Gra~o turned to three suppliers to propose solutions within their budget. Technicians from Martin Engineering examined every component of the conveyor system, from efficiency to safety and discovered that, due to the height of the transfer chute, dust created by the impact of material was most turbulent at the loading zone. When cargo hit the belt, pressure within the loading chute increased, pushing particulates at a high velocity out of any gap that was not sealed. Moreover, because of inadequate cleaning of the belt’s surface at the discharge zone, fines clung to the belt causing carryback on the return side, which led to spillage and dust along the entire conveyor path.
The result was large amounts of fugitive dust in the area, reducing air quality and visibility, settling on all surfaces and fouling rolling components. Seizing idlers contributed to belt mistracking and spillage, further increasing operating costs for cleaning, maintenance and downtime.
Technicians made a series of transfer point recommendations for controlling air flow and reducing carryback, which is essential for decreasing dust emissions. After preparing a detailed report and proposal, T-Gra~o managers agreed that a total transfer point solution was needed. Beginning with a tail sealing box, the solution included a skirt board cover, dust bags, impact cradle, slider cradles, track-mount idlers and a belt tracker, completed by a heavy-duty belt cleaner.
Heavy duty belt cleaner in action
Controlling airflow
Uncontrolled airflow and improper sealing through the loading and settling zone is the main culprit in the creation of dust and spillage in the transfer area, and it starts with the tail pulley. Protecting the tail pulley is important, because fouling of the pulley’s surface can lead to belt slippage and drift as the belt is entering the loading zone. Uneven loading worsens mistracking and breaks the belt seal with the skirt board, causing serious spillage and dust emissions. Installed on the rear of the chute work, the tail sealing box effectively stops dust emissions from the rear of the chute, protecting the pulley.
A vital component of the design was containing, lengthening and increasing the interior space of the settling zone. Along the entire length of the chute is externally maintained skirting, mitigating dust emissions and spillage due to turbulence and cargo shifting. The cover placed on top of the skirtboard reduces environmental problems posed by ‘shedding’ debris and material by enclosing it in a safe area away from moving parts. The structure controls airflow so fine particulates are directed toward the two dust bags installed above the chute, while heavier airborne dust is given space to travel and settle without leaving the chute environment. Material entering the dust bag is retained until the airflow subsides enough for the bag to relax and the load to drop back onto the belt.
The EVO® Skirtboard Cover is shown with two dust bags.
To control the turbulent pressure buildup from material dropping onto the belt, the heavy duty impact cradle features a top layer of slick UHMW polymer moulded to a base of impact-absorbing SBR rubber, all reinforced with a steel support structure able to withstand as much as 17,000 pounds (53.4 to 75.6kN) of force. Suffering no abrasive damage to the edge as the belt glides over the polyurethane bars, the cradle protects against impact wear on the belt and mainframe, with no rolling components to break down, which reduces maintenance and prolongs operational life.
Extending from the impact cradle down the length of the settling zone are cradles that slide in and out for easy maintenance while retaining a tight belt seal and a smooth path though the settling zone to mitigate dust creation. Using a smooth UHMW ‘box bar’ engineered to prevent heat buildup, the unique design provides dual-wear surfaces for extended equipment life. By supporting the edges of the belt to eliminate sag, the cradles prevent spillage, stabilizing the belt’s path and helping the skirting retain a tight seal. To offer further belt support, supplemental idlers are placed in the tight spaces between cradles to retain a straight belt profile, preventing ‘pinch points’ that can damage the belt over time and sag points that allow spillage. Utilizing sliding frames on a stationary base, rolling components on the idler are easily installed and serviced.
After the belt leaves the settling zone, a modern tracking system controls belt mistracking caused by uneven cargo. Using a rotating troughed idler connected to sensitive extension arms with rollers that ride both sides of the belt edge, the unit detects slight variations in the path and adjusts the idler before the belt drifts. Precise alignment keeps the belt from contacting the mainframe and causing edge damage and spillage, ensuring that the belt properly enters the discharge zone for optimal cleaning.
To conclude the project, technicians installed heavy duty belt cleaning system with a primary blade and spring tensioner designed to keep a tight seal across the blade profile with minimal wear on the belt or splice. Utilizing a curved blade design, the system maintains the most efficient cleaning angle through the life of the blade. Mounted with a minimal footprint on the mainframe, the cleaner improves discharge of fine material, reducing carryback, spillage and dust emissions along the return path.
As a compliance measure, technicians also installed safety guards along the system to prevent reach-in hazards. To inspect and monitor the operations of the system, sealed access hatches allow safe observation and maintenance of components.
Results
When the system was activated, operators immediately observed significant results. As material moved through the system, particulates remained within the enclosure and either collected in the dust bag or settled back into the cargo flow. Along with less carryback on the return side of the belt, dust was drastically reduced in the immediate area around the conveyor system at both the loading and discharge zones.
“It was a substantial improvement over the previous design,” Pina said. “The staff no longer needs to wear protective gear just to enter the area, and visibility is improved.”
After a lengthy observation period, operators report that there has been less downtime for cleanup and maintenance, as well as improved workplace safety. In addition, managers have enjoyed a reduction in complaints from neighbours and less scrutiny from authorities inspecting the port for air quality.
“Our dust control efforts have set an example that is now being considered by terminals up and down the port,” Pina concluded. “We are now planning to install a similar design on several of our other transfer points.”
Martin Engineering is a global innovator in the bulk material handling industry, developing new solutions to common problems and participating in industry organizations to improve safety and productivity. The company’s series of Foundations books is an internationally-recognized resource for safety, maintenance and operations training — with more than 20,000 print copies in circulation around the world. The entire 500+ page volumes can also be downloaded as free PDFs from the Martin website. Martin employees take an active part in ASME, SME, VDI, CMA and CEMA, and the firm played a pivotal role in writing and producing the 7th edition of the CEMA reference book, Belt Conveyors for Bulk Materials.
Martin Engineering products, sales, service and training are available from 18 Martin facilities, including factory-owned business units in Australia, Brazil, China, Colombia, France, Germany, India, Indonesia, Italy, Mexico, Peru, Russia, Spain, South Africa, Turkey, the USA and UK.