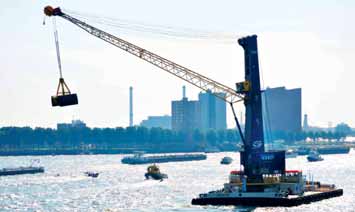
Port of Amsterdam achieves corporatization
The Port of Amsterdam has finally been corporatized, freeing managers to more easily access financial markets and fund investments both at home and abroad, writes Michael King.
Port managers have long been pushing for the change in legal structure which was finalized on 1 April. Although the Municipality of Amsterdam will remain the port’s single shareholder, instead of being a municipal service company the Port of Amsterdam has now been registered as a public limited company.
“This means we are able to act quicker and more market oriented,” said Lex De Ridder, commercial manager for bulk cargoes.
The legal change is highly significant in how the port develops in the future. Despite all its success over the last decade, port managers have been hamstrung in terms of identifying new ways of generating income because, as a municipal service company, they had to largely comply with public law. Corporatization via the creation of Havenbedrijf Amsterdam NV means managers are now only constrained by the parameters of private law, opening up new partnership opportunities.
In future, other public authorities such as regional authorities may also be free to acquire shares in the company and the new structure will also allow easier access to financial markets.
The strategic focus as Havenbedrijf Amsterdam NV will be two-fold: to optimize operations in the region of Amsterdam and its hinterland through further partnerships with other maritime facilities and ports; and to seek out profit generating port investment opportunities further afield.
“We will be taking a much broader look moving forward,” said De Ridder. “So we will continue to push for improvements in our competitive position here to maximize earnings in our port region by exploring new ways of generating money, but we will also identify new opportunities. This can be in The Netherlands as well as abroad.
“This could mean for example co-investing on projects in West Africa, South America of the Baltic area, for example.
“We have good connections in West Africa in places such as Ivory Coal, Ghana, Nigeria and Cameroon due to our cocoa business.
“We are looking for opportunities to co-operate and develop ports. If they’re connected to Amsterdam’s current cargoes, that is good. But the first aim is to look for interesting investments and now we’re corporatized we can do this.”
The port will be able to largely utilize its own capital after boosting revenues throughout the global financial crisis. Additional finances will be raised from traditional financial sources such as pension funds and banks. “We didn’t make a lot of new investments in the last three
years, so we have our own capital we can draw down,” said De Ridder.
The first priority will be the construction of a lightering station, to be located at a harbour on the North Sea at Ijmuiden. This will enable two Capesize vessels to be handled simultaneously, doubling current capacity at a cost of some €100m. A further €700m is earmarked for a new locks system at Ijmuiden which will allow direct access to the port of Amsterdam for Capesize vessels within the dimensions of around 17 metres draught, 65–70 metres beam and 500 metres in length.
“The whole project of the locks and lightering facilities is in full swing,” he said. “Legislation and all environmental licenses are in process now so we are almost ready to start.”
Construction of the lightering facility will start next year and should take two years to complete, while the new locks will be in place by the end of the decade.
“This will take some of our investment capacity, so if we want to make the next move then we have to go the banks and pension funds to attract risk capital,” said De Ridder.
While many ports in Europe struggled last year, Amsterdam performed well, posting volume growth of almost 3%, mainly to the good performance in the energy sector.
“It was a good year in the end. Oil products did well but agribulk was a bit slower, and building materials fell,” said De Ridder. “Energy is the big difference for us. We were on for a coal record until a strike at EDF, so in the end we were level year- on-year. Without the strike, growth would have been about 5%.”
Energy markets have seen major ructions recently which has had a significant impact on trade flows and long-term forecasts for Amsterdam. The widespread extraction of shale gas in the US has forced mining companies to push exports more aggressively, while the closure of coal mines in Germany, along with a pull back from building nuclear power stations following the Fukishima nuclear disaster in Japan in 2011, have changed the outlook for coal imports at Amsterdam.
“The market for coal in Germany looks quite good now,” said De Ridder. “It looks really positive that it will remain at least at current levels until 2024 and there could even be some growth. After that we don’t know. Coal could still be important, but gas could take over if shale gas gets developed in Europe on a mass scale.
“Last year we had three million tonnes of imports of coal from the US, but Colombia is still the dominant source here. US exports aren’t an extreme trend yet, but compared to three to four years ago, we’re receiving four times as much.
“Another interesting trade has been biomass. We’re now seeing this coming from Italy and the UK where they don’t have the capacity to process it. It’s used here as a feed stock for electricity production.”
New regulations currently under discussion in the Netherlands could give the biomass business a further boost, with terminals such as OBA eyeing the market for potential growth. “In the second half of this year there will be a decision on biomass burning regulations which could mean a subsidy for its use, or the obligation that companies use it for electricity generation,” said De Ridder. “Companies could be obliged to co-fire power stations, which could mean more biomass, perhaps up to 500,000 tonnes extra a year.
“If that happens then there could be lots of investment at big energy terminals, but also some of the companies dealing with soft commodities like cocoa and sugar are looking at this market, so depending on what happens there could be a big investment boost.
“We already have two dedicated biomass terminals planned and financed and ready to take off. Building will start in the second half of the year. One is already connected to Cargill’s plant and another will be developed and operated by Eucocorp in 2014.”
Amsterdam’s co-operation with other ports in the Netherlands is also continuing, particularly with Rotterdam. As well as both ports jointly exploiting the Betuweroute rail link to the German border, the ports also now have a fully operating IT system called Portbase, which registers all cargo and customs information in one huge data base.
The Port Community System covers all port sectors and supply chains including those used for bulk cargoes to reduce costs and improve information access and service provision. “Everyone uses this now, it’s going really well,” said De Ridder. “For bulk shippers it give us the opportunity to monitor cargo and intermodality in the hinterland much better, right through to Germany from both ports.”
However, the two ports still compete for cargoes ferociously. “We co-operate on promotion, and the relationship is very good, but we still compete and that will continue. In some markets there is excess port capacity such as containers and perhaps liquid and dry bulk in the years ahead so that competition will remain. It’s healthy competition.”
Rotterdam rides out tough conditions with new market opportunities
Rotterdam expects new markets to help boost forward demand as traditional sectors face hard market conditions, writes Michael King.
Regulatory reforms across Europe’s power sector are set to drive demand for biomass in the year ahead and managers at the Port of Rotterdam expect to win a sizeable share of the new business.
The port recently commissioned the Copernicus Institute of the University of Utrecht to study the biomass market and its forward potential. Analysis revealed that at present demand for biomass in northwest Europe amounts to some 44mt (million tonnes). And while Europe is still largely self-supporting, imports already amount to 4mt.
International trade in biomass is conducted mostly in the form of wood pellets, and the study found that demand for tradable wood pellets will grow to a maximum of 70mt in 2030. “This means that Europe will become more and more dependent on imports from other regions like Canada, the United States, Brazil, Russia and the Ukraine,” said the study, which predicts that feedstock hubs will develop in Europe around supply chain centres such as key ports.
“The Port of Rotterdam is perfectly positioned for this, in part because the port and the industrial complex already process these materials,” said the study.
This could see Rotterdam handling up to 15mt of wood pellets by 2030, from one million tonnes at present.
Abengoa Bioenergia already operates a bioethanol plant at the port and Karel Peters, Senior Business Manager Dry Bulk Industry & Bulk Department, said the Dutch government was currently debating new regulations for biomass use at power stations which could potentially be a big boost to trade. “We expect a decision this year, but we are also looking to other countries such as Britain where the government is supporting biomass and the conversion of power plants to full-biomass firing,” he said.
“We expect investments in the biomass business especially as power plants in England will need ports to handle and stock biomass.
“Several terminals are looking at this market and we hope to win a big part of it.”
Last year Rotterdam’s leading bulk stevedores handled some 73mt of incoming dry bulk, down 7.8% year-on-year, and 5.7mt of outgoing cargo, a decline of 27.4% compared to 2011.
A poor harvest due to drought last year in the Americas saw imports of agribulk cargo contract 17% in 2012 to just over 7mt. Peters said oils, seeds and bean imports were most affected. “It was a bad harvest in South America and it was dry in North America also,” he said. “The feed industry looked for compensation with grains and rapeseed but still, the volumes were less.”
Even so, Cargill is still expanding its facility in the Botlek area of the port by 28,000m2. Earlier this year the company’s sea
jetty was relocated enabling ships over 200 metres long to access the jetty directly, simplifying terminal logistics and boosting capacity at its vegetable oils and fats refinery in Rotterdam, one of the largest in Europe.
The travails of Europe’s steel industry also inevitably hit Rotterdam during 2012. Iron ore and scrap imports declined 10.6% to see volumes plunge to 30.8mt, although Peters said the port’s decline could have been worse given that European demand for steel products was some 20–30% lower in 2012 than in 2011. Volumes to VoestAlpine’s Austrian facilities did, however, remain stable, via Rotterdam, with incoming volumes transhipped to barges headed for the port Duisburg from where the cargo is loaded onto rail wagons for onward transportation.
Rotterdam’s ability to handle the world’s largest ships, including the massive Valemax fleet of vessels operated by Brazilian mining giant Vale, has been a key factor in keeping iron ore volumes relatively buoyant in the face of the stiff headwinds faced by the steel sector. “Seventy-five per cent of our iron ore comes from Brazil and 25% from other countries like Canada and when it’s sourced in Brazil we see a growing amount of calls of Valemax ships.We are seeing more of them,” said Peters. “That’s an advantage for us because we are the only port that
can receive these vessels fully loaded. EMO and EECV can both handle them.
“In the first quarter of this year iron ore volumes increased by 500,000 tonnes. Partly this was to do with restocking, but we’re also winning transshipment business with Valemax ships coming here before being transshipped to smaller vessels to ports such as Bremen, Ghent and Dunkirk. Last year iron ore for Dunkirk went direct, but the use of Valemax ships can change this so we hope to become a hub for other ports.”
As for all of Europe’s leading bulk ports, future demand for coal remains a key factor in dry bulk demand and one shrouded in mystery as various governments weigh up forward energy demand and how to meet it in the face of environmental policies that favour alternative sources of power. Energy price is also a key factor in long-term projections, with the potential of shale gas development in Europe, and the greater availability of coal
from the US where shale gas output from fracking is already having a huge impact on power generation, muddying the forward demand waters.
“On the one hand we expect growing imports because of the closing of German coal mines so they will need more imports,” said Peters. “In Rotterdam we also have two new coal-fired power plants coming into operation at the end of this year, operated by E.on Benelux and Electrabel/GDF Suez respectively. These plants is, depending on occupancy and co-firing of biomass, will require about 3mt to 4mt of coal annually, supplied via EMO’s facilities. So imports of coal will grow. “In Germany there were a lot of projects for coal-fired power plants, but a lot of them have been postponed or are cancelled. But there are some new projects which are already in operation or will come on steam this year — for example, Trianel’s plant at Lünen, STEAG at Duisburg and EnBW at Karlsruhe.
“But next to the social resistance against coal-firing the problem is that coal has to compete with wind and solar power so it depends on the price of coal in the future.”
More imports are also now arriving at Rotterdam from the US, he added. “What we see in the US is the gas price is very low, so production of coal is not used there but exported, and the price is attractively low so we are getting more imports,” said Peters.
“There are lots of factors that influence coal imports - price, stock, demand for energy etc. But we expect growing demand in the short and medium term.”
Both EECV (coking coal) and EBS (steam coal) have extended their dry bulk handling capacity in recent years, and EMO will do the same on the Hartelstrip from 2015. Peters said EECV was now receiving met coal from other Dutch ports and was onward shipping them to blast furnaces in Germany. “EECV is owned by ThyssenKrupp Steel Europe and they prefer to use their own terminal to supply plants,” he said.
Looking forward to the rest of this year, Peters is optimistic. In the first quarter Rotterdam handled 109mt of cargo across all sectors, down 1% compared to a year earlier. However, although coal volume fell due to stock at terminal being cut back, and agribulk was also down, iron ore and scrap volumes increased 10% to push dry bulk throughput to a 4% increase year-on-year to total 20mt.
“We now have enough capacity to cover rising imports of coal, we expect growth in biomass and although iron ore is expected to fall due to the general market, we are winning transshipment cargoes,” said Peters. “We are moderately optimistic about 2013.”
Ovet invests in rail to improve coal shipments to growing German market
Ovet is investing in its rail capacity as the stevedore expects coal import volumes destined for Germany’s coal and power sectors to continue to rise.
At the start of July the handler will open a new train loading facility at its Vlissingen terminal. This will enable trains as long as 44 wagons to be loaded in 2.5 hours, an undertaking that typically means lifting and loading around 2,700 metric tonnes net weight.
Sander van der Veeke, Account & Planning Manager at Ovet, said as Germany closes mines and pulls away from building new nuclear power stations, more coal imports will be required and the new capacity will aid in handling growing demand. “The train loader offers us more flexibility in modality for the German market,” he said. “At this moment we can only offer barge loading to customers. We are not able at this moment to play an important role in the German market. We believe that with the train loader, we can.
He said the rail carrier or shipper would usually decide on the routing to final destination by rail and this might not always involve using the Netherlands’ dedicated freight railway, the Betuweroute.
“DB Schenker will make use of the Betuweroute, others would use the Brabantroute (Eindhoven – Venlo) and another is thinking of Vlissingen – Antwerp- Ardennes – Luxemburg – South-Germany,” he told DCI.
Last year the port handled some 8.6mt (million tonnes) of ‘solid fuel’, a definition that takes in thermal and met coals, plus petcoke and anthracite. Ore volumes totalled 1.3mt with ‘miscellaneous’ cargo accounting for 0.2mt.This year some 10mt are expected to pass over its quays, said Van Der Veeke.
Unlike the ports of Amsterdam and Rotterdam which receive a large chunk of their coal imports from Colombia, Ovet’s Terneuzen and Vlissingen facilities mainly receive met coal from Australia, steam coal from Russia with imports from the US a growing feature.
Biomass has been handled at the port since 2005 and Ovet now boasts a 30,000m2 warehouse with six closed fully ventilated compartments designed specifically for its handling. “We have special grabs for the handling of biomass (36m3). We transport the cargo by tipper trucks from the quay to the warehouse,” said Van Der Veeke.
As other ports in The Netherlands point out, however, forward demand from Dutch power stations is now in doubt as the government debates whether to renew subsidies for the sector.
“Since 2009 the handled volume has been decreasing due to more competition and power stations invested in their own logistics facilities,” said Van Der Veeke. “The biomass market in the Netherlands is subsidy driven. At this moment the subsidy fund is finished, so no imports will be coming as of summer 2013. Without subsidies it is not a profitable business.”
ZHD Stevedoring: new 50-tonne floating crane operational and new-building of 50,000m3 warehouses has started
In order to further strengthen its position in the Rotterdam Rijnmond area and keep on serving its customers in a modern and professional way, some 20 million Euros have been invested at ZHD Stevedoring throughout the last 2 years.The Rotterdam based (family owned) private company with more than 40 years of stevedoring experience, is – even in these difficult market- situation within Europe - still working on a major investment program for the next 5 years.
MILESTONES IN 2011 - 2013 WERE:
- a new mobile Gottwald crane (HMK 6407B, High Tower), which has been operational in Dordrecht since April 2011;
- upgrading loading and discharging facilities for waste materials at Moerdijk, May 2011;
- a new 150m-long quay wall (Mallegat Quay Dordrecht) — opened in June 2011;
- 20,000m2 of newly developed storage area at Dordrecht — opened in December 2011;
- a new 50-tonne self-propelled floating crane — operational as of July 2012 and presented as highlight during the World Port Days in Rotterdam;
- ZHD has been GMP+ certified — December 2012; and v the new building of covered warehouses, with a capacity of approximately 50,000m3 — operational from August 2013.
Although the start of 2013 was not that positive due to difficult market circumstances, ZHD Stevedoring has decided to keep on investing in 2013. Mid 2012, ZHD Stevedoring has started the preparations for the construction of covered storage in Dordrecht. On 3 May, the new building started and the warehouses are expected to be operational in August 2013. “The demand for covered storage from both existing as well as potential new customers has been high in 2012,” says Leo Lokker, commercial director at ZHD Stevedoring. “By investing in covered storage facilities we expect and trust to serve our customers even better. The same goes for our new self- propelled 50 tonnes floating crane which is now operational in Dordrecht, Moerdijk and — of course — Rotterdam.” This new self-propelled 50-tonne floating crane further expands ZHD Stevedoring’s crane capacity and already has proven to increase performance and service of ZHD Stevedoring.
As of 1 July 2011 the municipality of Dordrecht and the Rotterdam Port Authorities have entered into an agreement to bundle forces, which was formalized in January 2012. This implicates that of this date (officially) the Port of Dordrecht has become an integral part of the Port of Rotterdam with all its benefits. Although already being active in Rotterdam for many years, by means of its self-propelled floating cranes, ZHD Stevedoring recognizes the advantages being part of the Port of Rotterdam. In close co-operation with the Rotterdam Port Authorities, ZHD Stevedoring is looking into possibilities and started the negotiations to reclaim another 10 hectares of land at its terminal in Dordrecht. This 10 hectares will be connected directly to the water with a 750m new quay wall with a 9.45m. draught, able to accommodate vessels up to approximately 40,000 tonnes. ZHD expects to announce a positive outcome of these negotiations before the end of 2013, from which the preparation and construction of this huge project can be started.
Apart from handling products like minerals, coal, petcokes and seasonal products as salt, ZHD Stevedoring has been focussing on handling and storage in niche markets such as steel- scrap, biomass (woodpellets) and waste-materials. From 1 December 2012, ZHD has also been GMP+ certified, giving it the chance to play its part in the transshipment of agricultural products. Special services are offered in the field of breakbulk and the handling of bulk in/from containers (among others, minerals, scrap) — a global trend which will grow in the future — are not unfamiliar to ZHD Stevedoring and completes the handling portfolio of the stevedore. With its steel terminal in Moerdijk, ZHD performs handling of coils as well as other steel
products, such as wire-rods, steel bundles, etc..
Rotterdam-based ZHD Stevedoring is a family owned, private company with more than 40 years of stevedoring experience. ZHD is active in the total so-called Rotterdam- Rijnmond area, with terminals in Dordrecht and Moerdijk, but also with its (self-propelled) floating cranes in Rotterdam.The company offers services in bulk-, neo bulk-, steel products-, coils- and container handling, including warehousing and storage (open, covered and floating).
ZHD has both road mobile and floating equipment and is able to handle all kind of product.All ZHD terminals are able to work round the clock (24/7) and are ISO and ISPS certified. Furthermore, ZHD also has water-related sites available for further (industrial) development.
DAMEN Pontoons & Barges launches second DAMEN crane barge 6324
On 9 January 2013, Damen Shipyards launched, at its Chinese Nantong Yahua Shipyard, the second crane barge 6324 in a row. The CBa 6324 is designed for transshipment works in open waters and will be equipped with a Liebherr CBG350 crane, a proven design and well accepted crane in the transshipment market.
The second crane barge in the series (the first one is in outfitting stage in Rotterdam) will be completely outfitted at Yahua Shipyards. Both crane barges are built on speculation and a delivery time of March 2013 can be ensured for both crane barges. One barge to be delivered ex-Nantong China, one barge ex- Rotterdam.
The equipment used on board of the LRs registered barges is all of a reputable make to ensure a high quality and second hand value. For example, Caterpillar generating sets, Azque pumps, DMT winches, van der Leun electrical installation and the Liebherr crane are used while the paint system has been applied by International Paint.
The Damen CBa 6324’s main purpose is to be used as a transshipment barge, but it can also be used for container handling operations and salvage operations. In grab operation the crane can handle 35t at 36m and daily production can reach up to 30,000 tonnes, in hook operation the crane can handle 45t at 36m.
The barge has a huge amount of free deck space and the wooden deck is equipped with container fittings all over the deck. A day and night accommodation for 12 persons including spare spaces is standard, optional propulsion units can be supplied.
Royal HaskoningDHV helps prepare fully automated fly ash terminal
Vliegasunie delivers mineral raw materials (fly ash, bottom ash and gypsum) to the construction industry and civil engineering. In order to balance supply and demand,Vliegasunie has several handling and storage facilities in the Netherlands.
Since January 2013 Vliegasunie has been operating a new fly ash silo in Moerdijk. The new distribution station SMZ is a fully automated plant which receives, stores, mixes and expedites various qualities of fly-ash without on- site operators.
Barges are unloaded pneumatically and only require the skipper to connect to the intake system. The automation system receives information about the type of fly ash from the dedicated cable connection to the main office, and when the skipper identifies himself with a personal badge at the local operator terminal, the installation will store the fly ash in the right segment of the multi-bin silo. The different qualities of fly ash are blended to the required specification before storing them in the two large storage silos.
Underneath the storage silos truck loading stations are installed. The automation system receives information about the fly ash shipments from the dedicated cable connection to the main office. By simply identifying himself at the gate and the correct truck loading location with a personal badge, the truck will be loaded automatically and the manifest will be printed. Off-site monitoring by Vliegasunie, including cameras, allows a quick response in case of emergencies. Royal HaskoningDHV assisted Vliegasunie with the site selection, feasibility study, basic engineering, preparation of tender documents and assistance during tendering. After contract award, Royal HaskoningDHV carried out site supervision including start-up and commissioning.
Dunlop Holland forges ahead
At a time when so many businesses are in economic turmoil and talk only seems to be of austerity, closures and job losses, Netherlands-based Dunlop Conveyor Belting continues to forge ahead in just about every way imaginable. On 13 May, Fenner Dunlop chief executive officer Nick Hobson officially opened Dunlop Holland’s new steelcord production line, which is being used to produce steelcord belting there for the first time ever.
Sales and marketing director Andries Smilda already has eyes on winning new market share. “This will create a whole new dimension to our sales efforts. A great many of our customers use steelcord as well as rubber multi-ply belting so we have a ready-made target market to attack”. Up until now, supplies of steelcord belting for their existing customers have largely been produced by Fenner Dunlop Americas and Fenner South Africa. “The quality is excellent ” explains Smilda,“but with our own steelcord production located in Europe we are now able to be much more flexible and responsive to the needs of our customers. In fact we have already received orders from regions such as the Middle East and Africa that will fill the press for the next six months!”
The new production line is an integral part of the recent factory extension in Drachten and is able to produce steelcord belts. Technical director, Dr Michiel Eijpe, believes that it is one of the most technologically advanced and efficient steelcord production lines in the world. “Thanks to the help and experience of our colleagues around the world of Fenner Dunlop, we were able to build in several enhancements that make this line super efficient.”
The first belts have already rolled off of the presses without a single fault. “To achieve that level of quality at the first attempt on a brand new production line of any kind is virtually unheard of” he continued. “It certainly justifies all of the very detailed planning and preparation work that went into the project.”
Steelcord production can be immensely complex. For example, on a 1,600mm-wide belt, there are 142 steel cables that have to be fed simultaneously (and very precisely) into the machine. To make loading more efficient than the usual method of using a loading robot, a special, Dunlop Drachten designed feeding belt has been installed in the creel (the rack holding the spools of cable), which carries the spools towards the correct position in the rack. While this is all happening the position of the second ‘deck’ has been designed to allow the operators to prepare the next set of cables to achieve an almost uninterrupted production flow and thereby significantly reduce lost production time.
DUNLOP SERVICE HOLLAND CONTINUES NETWORK EXPANSION
Not content with expanding its production capacity in Drachten, introducing steelcord production for the first time ever and investing heavily in upgrading their laboratory and R&D facilities, the Dunlop Service network is also being expanded at a rapid pace. Following its recent opening of a new sales office and warehouse in Dubai, Dunlop has even more recently opened a new Dunlop Service outlet in Ghana to cater for the needs of the West African market. The decision to go ahead with what is seen as a strategically important move was driven by the economic growth in the region over the recent years, plus positive developments in the mining and petroleum sectors. The new company, ‘Dunlop Conveyor Belting Ghana Ltd’, is based in the capital, Accra.
Phase one is now complete with the new office now functioning and further recruitment is taking place to strengthen the team. Phases two and three are already underway to create a warehouse for conveyor belt stock together with a workshop facility for the service team. The aim is to be fully functional by the end of the third quarter of 2013. The management team in Ghana is confident that they will bring rapid growth to the company and further strengthen the already renowned Dunlop reputation for quality. “We have already had a lot of very positive feedback from customers, including those in the mining, and quarrying industries” says regional manager James Cammock. “The fact that we are the very first conveyor belt manufacturing company to establish such a physical presence in the region has been very well received and much appreciated by the local market” added Cammock. “Taking our business to the customer and providing added value and services rather than trying to work at a distance from The Netherlands will make us stronger than ever. We are very excited by the challenge and looking forward to putting Dunlop even more firmly on the map in West Africa.”
These latest investments are proof positive that this is certainly one Netherlands-based company that is not prepared to sit back and wait for things to pick up. Dunlop’s management maintains that more and more companies are beginning to realize that spending a little more for higher-quality belts that provide a much longer working life is a more effective way to reduce their conveyor running costs rather than opting for short-term, apparently low-price solutions. “The world economic situation, especially in Europe, is a big challenge,” says managing director Edwin Have,“but economic recessions also provide opportunities for those who are prepared to invest and innovate rather than cutting costs by compromising on the quality of the product. So that is precisely what we are doing.”