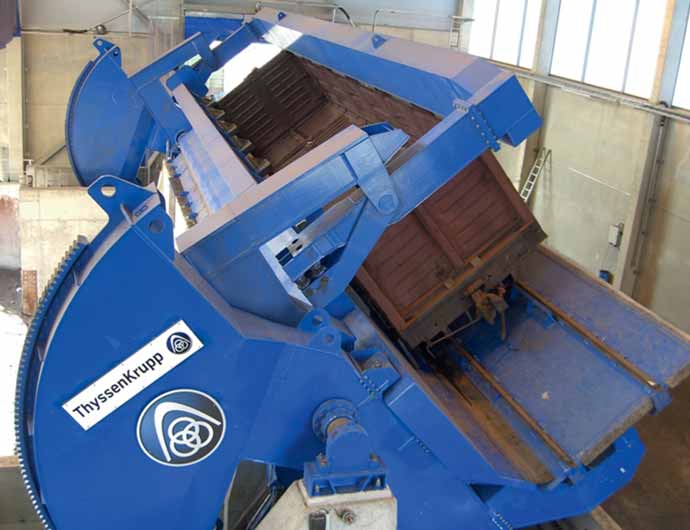
ThyssenKrupp Resource Technologies (TKRT), a division of ThyssenKrupp Industrial Solutions South Africa (Pty) Ltd, delivers end-to-end equipment solutions for bulk materials handling.
“From extraction at pit side to export at port side, we are positioned to offer best-in-class technology and system design solutions for efficient bulk handling solutions,” says TKRT sales manager, Matthias Göing. “Our comprehensive range of bulk materials handling equipment includes excavators, crushers, feeders, conveyors, stackers, reclaimers, transfer cars, as well as train and shiploading and unloading systems.”
“An operation is only sustainable if it is profitable,” continues Göing. “We fully comprehend the importance for customers to achieve maximum efficiencies through optimum production while keeping input and operational costs to an absolute minimum. Large capital investments made on equipment has to be weighed against operation efficiency and productivity to achieve profitability. So we do not just supply equipment. We look at the operation holistically, from an in-depth analysis of the customer’s requirements to the design and development of an optimized system.”
According to TKRT engineering manager, Carel van der Merwe, correct equipment selection plays a crucial role. He points out that in order to ensure best equipment choice, numerous interrelated factors such as operation lifespan, mine yield, capacity requirements, material characteristics, blending requirements, equipment compatibility, etc. must first be taken into account. “To ensure that all these factors are dealt with to achieve maximum efficiencies demands extremely detailed planning and organization. This does not commence at the pit face as one might think, but at the end of the process i.e. working backwards from port side to pit side,” continues Van der Merwe and explains,“The material quality required by the end user, the shiploading capacities demanded by the port as well as the size and loading requirements of individual ships must all be factored in. Multiple factors along each step in the process must also be analysed to ensure best-fit equipment selection.” Van der Merwe adds that during equipment selection one must bear in mind that a mine is not static and is constantly evolving. “As the seam progresses, it moves further away so the equipment must also be able to handle these changing dynamics to ensure continued efficiencies.”
Van der Merwe says material types play a crucial role when selecting suitable equipment for the first step in the process i.e. material excavation at the pit face. “Hydraulic excavators are recommended for selective coal excavation and compact mining applications while the higher production efficiencies offered by bucket wheel excavators make them preferred choice for continuous block mining in larger mines.”
“Next comes the choice of transport systems required to move the excavated material to run-of-mine [ROM] crushing stations. “Mine life determines transport system decisions,” continues Van der Merwe. “While shiftable and extendable conveyors significantly reduce operating costs, they are less flexible than trucks and more costly. Mobile conveyors are ideal where more flexibility is required but the capital costs are higher. For large operations and long distance materials handling, fixed overland conveyors provide the best solution in terms of both capital and operating costs but limited flexibility is the compromise. In some mining applications such as continuous block mining and where mine life is ten years plus, equipment combinations such as trucks feeding shiftable and extendable conveyors, coupled with fixed overland conveyors to handle the longer distances, will deliver a good balance between flexibility, high production and low operational costs.”
Upon reaching the crushing stations, the material is fed into the crushers by feeders at a controlled flow for processing. Best feeder unit choice depends on material composition and required throughput. The TKRT feeder range includes reciprocating plate or push feeders (ideal for large lump sizes and low capacities); rotary plough feeders; grizzly screens (best suited to higher capacities but unsuitable for sticky material) and apron feeders (controlled and continuous feed at high capacities and suitable for feeding very large lumps). “We also supply a wobbler feeder, which, like the grizzly, combines feeding and screening, but it can handle sticky, moist material such as coal at medium to high capacities,” notes Van der Merwe. Göing discusses the advantages of TKRT’s various crushing equipment solutions.“We provide stationary crushing plants, semi-mobile crushers which can be moved to a new location as the mine expands and finally, fully mobile options. The fully mobile crushing plant travels behind the excavator and, as it is loaded directly from the excavator and only then onto a truck or transport conveyor, the need for double handling is eliminated.”
TKRT roll crushers or sizers are suitable for soft to medium/hard material at high capacities. Jaw, gyratory and jaw gyratory crushers are ideal solutions for hard materials with large in-feed sizes, large reduction ratios and at medium to high capacities. “We also offer a high capacity jaw-gyratory crusher that operates on a progressive crushing principle for handling hard material and very large in-feed sizes. These crushers are similar to gyratory crushers, but with a flared inlet geometry for handling of larger lumps.
Stockpiles are normally required between the mine and the port. Van der Merwe says that the selection of suitable stockyard equipment (stackers and reclaimers) is closely associated with the specific purpose of the stockpile. “Big storage, small buffer stocks and/or blending will determine the stockyard type which includes longitudinal, cone, kidney, circular, bunker, etc. Again it is best to start at the shiploading process where consideration of port storage facilities, product grades/types, reclamation rates required to load the ships and delivery requirements for material from the mine will determine preferred equipment,” he adds.
He further recommends to first select the reclaimer before considering the stacker and stacking method. “In addition to the already-mentioned stockyard type, other factors that determine reclaimer selection include lump sizes, material flow-ability, capacity (tons per hour), blending requirements, need for reclaimer to pass over adjacent stockpiles, etc.” The TKRT range of reclaimers include drum, portal, side arm scraper, bridge-type scraper, half-bridge-type and bridge-type bucket wheel and boom- type bucket wheel and plough feeders. “South Africa is the global ThyssenKrupp group’s centre of excellence for drum reclaimers. While drum reclaimers cannot pass over stockpiles, they offer high capacities of up to 5,500tph (tonnes per hour), even output, excellent blending and suitability for free flowing, sticky or lumpy materials. For applications which require passing over of stockpiles, portal and side arm scrapers are recommended as well as bucket wheel reclaimers. Bridge bucket wheel reclaimers are more suitable for use with sticky materials and offer high, but fluctuating, capacities. For high capacity reclaiming of several products/grades with no blending requirement — which is typical for ports — ThyssenKrupp offers the boom type bucket wheel, which is suitable for all material types.”
Stacker types from TKRT include luffing, slewing and luffing combination, wing, radial and overhead stackers. Van der Merwe says that blending is the dominant criterion for the selection of a reclaimer and stacker combination. “Windrow stacking — which requires a slewing and luffing stacker with a longer boom — can increase the blending efficiency when reclaiming with a boom type bucket wheel machine, but offers no benefit when combined with bridge scraper reclaimers and drum reclaimers. Likewise strata stacking improves blending only when used in combination with portal scraper reclaimers”
Discussing TKRT’s train loading solutions,Van der Merwe says that high capacity operations conduct train loading in motion. “The train travels at a slow speed underneath the loading station while a weighed quantity of material is loaded according to each wagon’s axle capacity. “We can also offer a less conventional loading solution that uses a conveyor with a tripper moving along the side of a stationary train, filling the wagons one by one. The most suitable loading system is determined by the loading rate that is required. At the mine, a load out station must be selected that can meet the rail operator’s cycle time and wagon type requirements. At port side, there are several equipment options available for train unloading including bottom and side discharge wagon tipplers, rotary and tandem rotary wagon tipplers.”
Finally moving to shiploading,Van der Merwe says that temporary shiploaders and container tipplers can be used for low to medium capacity shared facilities. “Dedicated systems are preferred for high capacity loading. While construction of radial type shiploaders and their supporting quays are more economical, they are only suitable for single berth quays and a specific ship size. Co-ordinate shiploaders (shiploaders that travel in a straight line, with a luffing and telescoping boom) can serve several berths and ship sizes on the same side of a quay. Travelling shiploaders with luffing and slewing boom offers maximum flexibility as they can be used on both sides of the quay and can load differing ship size requirements.”
In closing, Göing points out that TKRT, as an engineering driven company, delivers modern, world class, turnkey solutions which includes not only equipment supply but also excellent service throughout the lifecycle of a project or equipment. “Whether new projects, plant upgrades, refurbishments or improvements, our sophisticated systems are supported by highly trained and qualified service engineers and technicians offering product support, audits, inspections, technical advice, maintenance, repair, spare parts and components. We form a long-term partnership with our customers, working closely with them to optimize plant efficiency so they can reap the benefits of lowest total cost of ownership and a high return on investment.”