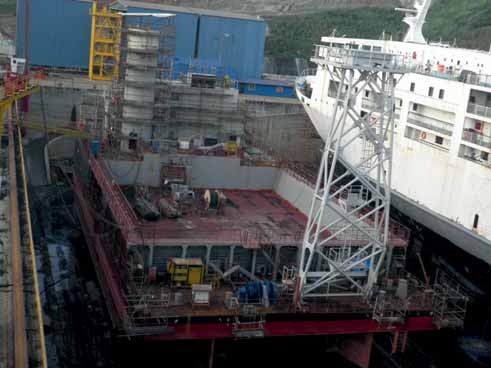
Grabbing attention: a customized approach for efficient supply chain solutions
After its work on the world’s largest floating hub (Ore Fabrica, which was commissioned in 2012 for the transshipment of iron ore for Vale), Logmarin Advisors then contributed to the implementation and commissioning of something very special, in 2013. This time, the project involved the world’s largest ‘octopus’ (orange peel) grab, which was manufactured in Germany by Peiner SMAG to handle woodchips in Indonesia.
The mega grab has a capacity of 56m3, roughly corresponding to one million golf balls!
The grab, mounted on a Liebherr crane with a lifting capacity of 45 tonnes, has been installed on board the floating crane Green Global which is carrying out transshipment operations handling eucalyptus and acacia woodchips in Indonesia.
Despite fierce competition in the transshipment market niche, four new floating terminals have been designed and commissioned during 2013, bringing the ‘Logmarin fleet’ to 19 units. In addition to these, two more units are currently being constructed: a Ratu Giok-type floating crane and a larger floating terminal withstorage,weighting,samplingandblendingfacilities with a daily average throughput exceeding 55,000 tonnes, which will be delivered in July next year.
This demonstrates that a solid knowledge of the markets, of the material to be handled — combined with technical and operational expertise — provide added value at the design stage, thereby leading ultimately to enhanced efficiency and competitiveness for clients.
Client satisfaction and retention is also demonstrated by repeat orders. The feedback received from ongoing projects is carefully incorporated into future designs. After the positive results of the floating crane Ratu Giok (Queen of Giade) Logmarin is now about to deliver the fifth sister to Indonesian owner KSA. Such results are not achieved by chance.
THERE IS NO ‘ONE-SYSTEM-FITS-ALL’ SOLUTION IN TRANSSHIPMENT OPERATIONS The wide range of commodities that Logmarin deals with includes the stickiest iron ore and bauxite, dusty coal, scented woodchips, grains and rolling iron ore pellets.
The experience gained in more than 20 years of technical and operational activity has taught that the concept of ‘one-solution- fits-all’ decidedly does not work in supply chain design.
Every project has specific features, and it requires appropriate care/design to be properly carried out.
That’s why Logmarin’s strategic approach to every supply chain project is successful: first of all, the company gains a deep understanding of clients’ requirements, and through continuous interaction and sharing experience with them it is able to offer tailored support.
The flexibility and customized solution is well represented in floating terminal market. Transshipment operations can be carried out by vessels with different features; some examples of Logmarin ‘type solutions’ follow:
- floating cranes Princesse Abby and Nicholas type, equipped with one or two grab cranes respectively. These are essentially cranes mounted on pontoons being used for the direct transfer of coal from barges onto ocean going vessels by berthing them between barges and ocean going vessels;
- floating terminal Princesse Chloe type, equipped with two cranes working in conjunction with the covered conveyor system and optional buffer storage on deck (9–12,000 tonnes of dry bulk cargo). In these types of floating transfer stations, the rotation of the cranes is reduced by way of installing hoppers to receive coal, which is then transported to the oceangoing vessels by a series of conveyors and a shiploader. The deck space can also be utilized as a buffer storage where cargo can be stored in order to have continuous cargo loading operations even when barges are not available;
- Panamax floating terminal Mara type, equipped with four heavy duty side-mounted cranes and able to perform blending operations and segregate different cargo qualities thanks to the 65,000-tonne buffer storage. These types of system are used where the scale of operation is much bigger and a bigger storage is necessary. There are two shiploaders (Bedeschi) installed on this system so that the warping of the system alongside the ocean going vessels in greatly reduced;
- floating hub Ore Fabrica type, equipped with five heavy duty cranes and a travelling shiploader, and with 285,000 tonnes buffer storage available on deck. This system is used to transfer iron ore from the Valemaxes into shuttle vessels.
Most of the floating terminals incorporate BLL (Bedeschi Liebherr and Logmarin) integrated solutions as shown on the front cover of this issue. Together Logmarin, Liebherr and Bedeschi have designed and implemented many innovative transshipment systems. They therefore decided to pool their efforts and form an alliance called Bulk Logistics Landmark (BLL). BLL is a strategic business alliance, profiting from the synergies of the three constituents. While continuing to do what each partner does, more efficiently, the pooling of skills and expertise of Bedeschi, Liebherr and Logmarin provides dependable, integrated, cost-effective software and hardware, and eco-friendly solutions in the dry bulk supply chain. BLL encompasses significant resources in terms of expertise, technology, network and expertise from its partners and associates, gained through years of experience.
In order to remain competitive in today’s market, it is not only essential to focus on one’s own line of business, but it is vital to rely on creativity and innovation, just as much as knowledge and experience, to ensure sound results suiting client’s specific needs/requirements.
To support clients in the decision making process during the development of a new supply chain or the improvement of an existing one, Logmarin has customized commercial software into a dynamic Supply Chain Simulation Software (LOG.DES) to analyse the key resources (links) of the end-to-end supply chain.
Logmarin simulates the entire supply chain thanks to Log.Des; the software aims at evaluating water transportation systems, identifying optimal loading rates, analysing river/sea navigation and defining cargo handling features and main supply chain bottlenecks.
This simulation process helps in better understanding the inherent risks associated with the mine to industry process and makes it possible to recognize/identify the optimal tailor-made supply chain solution.
To offer its customers a larger variety of products and services Logmarin can provide, together with Liebherr and Bedeschi, progressive advice (software) and reliable products (hardware). In Indonesia alone, four BLL systems are in operation, viz. Princesse Chloe,Vittoria, Mara & Zeus. The fifth one is under implementation and will be delivered in July of next year. In addition to coal projects, BLL has implemented various floating solutions for iron ore too, viz. Ore Sossego and Ore Fabrica for discharging and Shatixa and Chowpatlal for loading .
By pooling the individual skills, strengths and expertise of its member companies, BLL is able to define not only effective floating terminal solutions but also reliable shore terminal facilities.
An example of an upgrade to a shore terminal is the Toros project in Turkey, for which BLL designed two new travelling cranes, hoppers and a conveyor system.
The terminal is capable of unloading coal, petcoke and fertilizers from post‐Panamax vessels at a daily average rate exceeding 25,000 tonnes.
BLL provides a wide range of highly technical solutions: from a single product up to turnkey projects (including commissioning, crew training, after-sales support, etc).
More than ever, commodity supply chain design requires a complex and integrated multidisciplinary attitude: technical, financial, geological, operational, maritime, civil, logistics, environmental and fiscal backgrounds have to be led/coordinated by a ‘logistics mind’ in order to achieve efficiency, optimization and sustainability (see the front cover showing some of BLL’s successful projects).
BLL says,“We believe by working with the above strategy many more achievements can be grabbed together.”
New transshipment operations in Sierra Leone, thanks to LD Ports & Logistics
LDPL (LD Ports & Logistics) was appointed by LMC (London Mining), a London-based mining company to perform iron ore transshipment operations off Freetown, Sierra Leone.
The company has mobilized its latest Floating Crane Transshipper Unit (FCTU) Miramar, designed and built by LDPL in 2011. LDPL is able to guarantee a net loading rate of 20,500 tonnes per day to its client LMC.
The FCTU arrived in Freetown on 25 May on-board Transporter, a heavy- lift vessel which carried her from her previous area of operations in Goa, India. According to LMC Managing Director, this FCTU, the latest addition to London Mining’s fleet will provide a further improvement to the company’s export logistics capacity, relying so far only on London Mining’s Pride of Marampa, LMC’s existing Floating Offshore Transshipment Platform.
The additional loading capability provided by the FCTU will be of particular benefit during the wet season, and will be instrumental in continuing to achieve targets.
Miramar was commissioned on 1 June 2013, a few days after her arrival on site. She was able to load her first large gearless ocean going vessel with a consistent rate of 20,400 metric tonnes per day. LMC Managing Director concluded:“This is another significant development for London Mining and our Marampa operations. The arrival of this FCTU will allow London Mining to achieve safely our annual export target of over five million dry metric tonnes of iron ore concentrate,” he said.
LDPL FLOATING CRANE TRANSSHIPMENT UNITS (‘FCTU’)
At the brink of the 1990s, Louis Dreyfus Armateurs realized that the economic development of certain countries in South East Asia and South America would largely depend on port infrastructures.
In order to avoid costly fixed investments, which would only be possible under strong economic growth conditions, LDA developed an innovative solution to allow massive exports of dry bulk commodities from these areas. Thus, in 1989 LDA acquired and operated for Adaro its first Floating Crane Transshipment Units. For more than 20 years LDA has been operating floating cranes, acquiring an essential know-how in transshipment. LD Ports & Logistics floating cranes are the result of this extensive experience gained over these years.
LDPL’s FCTU are the result of a unique combination of all ingredients proven to be necessary to excel in the art of transshipment, blending simplicity and robustness. These features are essential to success in logistics operations conducted at sea and avoid maintenance operations, always extremely disadvantageous. By controlling the entire project processing, from building to operations, LDPL has managed to -
A similar spirit of innovation was used by LDPL to develop self- propelled barges, which represent the future of barging. Such vessels allow significant cost savings through larger scale and increased fuel efficiency, as well as improvements in logistics operations, whilst retaining shallow draft characteristics.
LDPL has developed a unique and innovative self-propelled
barge design, which, depending on its clients’ operations, can be fully customized to the needs and entirely built and operated by LDPL.
LDPL’s recently built self-propelled barges will carry 13,000t of coal between Kalimantan’s Tanah Merah Coal Terminal and Paiton Energy. They cover the 450NM journey at an average speed in excess of 9 knots, and generate significant fuel efficiencies by burning heavy-fuel oil instead of diesel oil. They will provide LDPL’s clients with better reliability for their supply chains, by removing the uncertainty of seaworthiness inherent to tugs and barges in challenging sea conditions.
TRANSSHIPPERS
Drawing from a wealth of experience in transshipment, using floating cranes, LDPL has developed a new design of Transshipper (Floating Transshipment Unit) to cater to the needs of exporters of large volumes of dry bulk cargo. This new generation of transshipper has been created to achieve unrivalled loading performance, whilst offering the simplicity and reliability of bulk loading system such as floating cranes.
Largest Damen Stan pontoon for McKeil-Malaspina
The largest pontoon ever stock-built by Damen was sold to the Canadian McKeil-Malaspina partnership and will be towed to Newfoundland on the East coast of Canada this summer. Upon arrival in Canada, the pontoon will be used to support offshore construction operations.
The Damen Stan pontoon 12032 measures 120m × 32.2m (400ft × 100ft) and has a deadweight capacity of approximately 20,000 tonnes (50,000 lbs) and a hold of 8.10 metres (27ft). The barge is equipped with a sophisticated ballast system, generating set, mooring winches and, with a deck load of 20t/m2, this barge can be used for complex RoRo operations and/or for transport of large offshore constructions.
Earlier this year Damen shipped 16 newly built pontoons from her shipyards in China to Damen Shiprepair Rotterdam. Most of the stock-built pontoons are sold, leaving only two Stan Pontoons and a Damen Transshipment Barge (including Liebherr crane) for direct sale. Early 2014 a new shipment of Damen pontoons is scheduled to arrive in the Port of Rotterdam to ensure short delivery times.
DAMEN SHIPYARDS GROUP
Damen Shipyards Group (est. 1927) operates more than 55 shipyards, repair yards and related companies worldwide. Damen employs 8,000 people in 35 countries, has delivered over 5,000 vessels since 1969 and delivers some 150 vessels annually to worldwide customers. Based on its unique, standardized ship- design concept and short delivery times, Damen is able to guarantee consistent quality.
Damen’s focus on standardization, modular construction and keeping vessels in stock leads to short delivery times, low ‘total cost of ownership’, high resale value, proven technology and reliable performance. Damen offers a wide range of products, including: tugs, workboats, patrol vessels, high-speed craft, cargo vessels, dredgers, offshore support vessels, oil-spill response vessels, frigates and super yachts. For nearly all vessel types Damen offers a broad range of Services, such as lifecycle maintenance services, customer finance, training and transfer of (shipbuilding) knowledge.
In addition to ship design and shipbuilding, Damen Shiprepair & Conversion offers a network of 16 ship repair and conversion yards worldwide, most of which are conveniently located along the North Sea coast from Brest (France) to Gothenburg (Sweden). Damen Shiprepair & Conversion operates 40 dry docks of all types and sizes and offers onsite/onboard repair services. Conversion projects range from updating smaller or older vessels to today’s requirements to the complete conversion or rebuilding of large jack-up rigs.
DCi