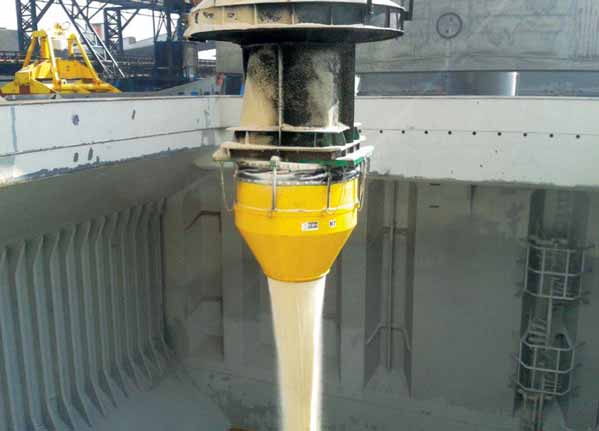
Loading bulk solids with explosive characteristics
Cimbria Bulk Equipment has serviced the dry bulk industry for decades, focusing on the loading and conveying of all kinds of industrial bulk goods. The company has thereby gained a vast experience within industrial bulk handling. This experience is constantly being put to use in developing new solutions which meet the demands of authorities and users for functionality, quality and environment friendly operation.
The solutions have been developed on the basis of a product range consisting of various types of loading chutes for open and closed loading of dry bulk materials into e.g. trucks, rail wagons, containers, ships and for stockpiling. The loading chutes are sold under the brand name Moduflex.
HANDLING EXPLOSIVE PRODUCTS
Dust is an important issue when handling various bulk products such as grain, feedstuff, flour, sugar, wood or other organic materials, as it can be the cause of great nuisance in the work place. Not only because it can have a harmful effect on the human body working in a dust laden atmosphere, but also because the storing and handling of these products always contains an explosion risk that might cause destruction of buildings and production equipment and in worst case - loss of human life. However, recent years increased focus on preventing dust explosions with the implementation of the ATEX-directive has proven to have a preventative effect.
The demands for explosion proof equipment imply that the whole machine should be suitable for installation in high explosive risk areas. This means that all relevant mechanical parts and electrical components are special constructed and certified for use in areas where ATEX-zones are in force. All precautions taken endeavour to create a safe working environment. Beyond the direct improvement of the working environment by bringing down the amount of airborne dust, the risk of a dust explosion — when handling such products — is thereby reduced to a minimum.
MEETING ATEX DEMANDS
Through the years, Cimbria Bulk Equipment has supplied loading and conveying equipment in compliance with different national and international regulations. With the introduction of the ATEX-regulations, Cimbria Bulk Equipment was the first manufacturer of loading chutes to get an ATEX- certification. Today, the company has a standard working policy to insure that the supplied equipment is in compliance with the rules laid down in the ATEX-directive. Not only are the individual parts scrutinized, but the complete working unit where all factors including preventing the build-up of static electricity and max. surface temperatures are taken into consideration.
Key words in connection with ATEX related equipment is approval, marking and documentation, where the manufacturer’s declaration plays a key role.
As a part of the approval of the Cimbria Moduflex loading chutes, is the compilation of a comprehensive technical dossier based on the mandatory risk analysis, which among other contains considerations concerning health and safety aspects in relation to the ATEX-rules.
SUPPLY OF LOADING CHUTE NO. 13,000
Due to the factors mentioned above Cimbria Bulk Equipment has already delivered many Moduflex loading chutes manufactured for plants where dust control, hygiene and compliance with the ATEX-directive are an essential prerequisite for the supply.
Cimbria Moduflex partner in Lithuania, Firma Liucija, has most recently placed an order for 8 Moduflex loading chutes of the type HDF400. Each loading chute is fitted on a positioning unit for optimal manoeuvring when loading rail wagons from the same silo battery. One of the ordered units is Moduflex loading chute no. 13,000, which has been supplied worldwide for numerous installations throughout the years.
These chutes will be used for loading soya beans and raw sugar, and due to the nature of the product the loading chutes are provided with explosion proof components in accordance with the ATEX-directive. The chutes are equipped with a 13,5m2 built-in filter that is fully self-contained with its own pressure tank, fan and diaphragm pulse valve. Furthermore, are the chutes equipped with six chute modules with antistatic strips and earth wire, which give the chutes an extended length of nearly 4,200mm.
Each loading chute is fitted on a FlexPositioner, a motorized positioning unit that ensures the right position of the chutes in relation to the rail wagon loading hatch. Instead of the rail wagon having to be stopped precisely under the chutes, the chute itself is manoeuvred by the remotely controlled positioning unit. In loading situations where a long train of rail wagons would otherwise have to be driven into a precisely determined position, the unit can offer effective saving in total loading time.
Cimbria Bulk Equipment supplies dust-free loading systems through a network of agents in more than 30 countries around the world.
Transshipment ports ‘demand’ eco-friendly grabs
The legal requirements for port companies in terms of bulk goods handling are becoming increasingly important with regard to emissions. The fact that many handling companies are situated in the vicinity of residential areas makes it all the more imperative to avoid environmental impacts such as dust formation and ground water pollution.
With 35 years of experience in loading and shipping practices, grabs expert Franz Lehnert, sales director at Kröger Greifertechnik, Sonsbeck, provides an overview of the necessary requirements on future-oriented, ecologically responsible loading grabs.
“Open the grab jaws. Grab the bulk goods.Transship. Things are no longer as simple in harbours and ports,” says Franz Lehnert. “Today it implies: grab the bulk goods. Do not lose any of it. Protect the environment.” This mainly applies to free- flowing bulk goods. ‘Free-flowing bulk goods’ primarily include aluminium oxide and ilmenite. However, closed grab designs are required in case of ‘normal’ bulk goods such as salt, slack, phosphate or animal feed (e.g. grains) as well in order to avoid dust formation. While open grabs were absolutely normal earlier, today one almost exclusively finds closed loading grab types in Europe. Winds occurring on water and in the harbours compel handling companies to appropriately protect their conical piles.
As a matter of fact, there are mainly three areas in a grab that need to work in an eco-friendly manner: the specifically raised grab jaws, the grab edges and the hinge bearings. Let us first consider the eco- friendly grab jaws. The grab jaws are raised above the angle of repose so that the often strong winds in harbours and ports are left with no chance to affect the conical piles and, consequently, the light, dust-forming bulk goods. Here Kröger speaks of a so- called ‘open bag’. Specifically, it means that the jaws remain open in the above area in order to avoid explosion during closing and, thus, prevent environment pollution. An ideal solution to the problem of blowing-off of goods.
Matters become more complicated during tight closing of the grab edges. This requires higher effort in terms of structure and design so that the grab jaws are able to operate as absolutely ‘watertight’ units even under extreme loads and continuous, long- term usage. This is because free-flowing bulk goods such as salts or phosphates need secure closing of the loading grabs. In 90% of the handling goods tight closing of grab jaws can be achieved by means of double Pantanax round-bar steels both on the bottom scrapers as well as the side blades. The jaws close tightly through the bedding in of both the linked round-bar steels until a watertight closure is reached.
However, in practice such free-flowing bulk goods are also transshipped that are more flowing than water: aluminium oxide and ilmenite are examples of such bulk goods, for which tight closing of grab jaws by bedding in the Pantanax round-bar steels is not sufficient. In this case, tight closing is achieved through a rubber seal. Here, an open profile from the opposite grab jaws presses into a replaceable rubber lip (foamed rubber with hardness number of 20 Shore) during the closing operation. The rubber fits up to one-hundredth of a millimetre into the open profile and, in this way, prevents loss of the special bulk load due to trickling. The rubber lip itself is protected against damage by means of a Pantanax round-bar steel mounted all around.
The term ‘sustainability’ is becoming increasingly important even for port handling companies, as trade supervisory boards are also continuously updating the requirements and imposing restrictions. Therefore, it is no wonder that from water and soil pollution right up to ground water protection everything plays an important role. We are talking about protecting the environment from oils, greases and lubricants. For this reason, all Kröger grabs are designed to be not just low-maintenance, but absolutely free of maintenance, i.e. they require no lubrication either during guiding the closing ropes and mounting the pulley, or while positioning the hinge bearings. The latter is yet another innovation of the Kröger ‘think tank’ that fulfills the requirement of environment protection in addition to achieving high cost effectiveness through longer operating life: old grease no longer ‘squeezes’ out of hinge bearings, old lubricants no longer end up in (ground) water. Undesirable follow-up costs are therefore a thing of the past, which is also seen in the daily endurance and critical tests in sea ports and inland harbours. Until now, for instance, the situation was that especially during salt and coal handling deposits would form on the lubrication nipples, making the work difficult and polluting the environment.
Kröger makes use of all three eco-friendly technologies with good experience not only in cable and motor-powered grabs, but also in the fast hydraulic grabs. When asked to comment on the eco-friendly loading grabs for harbours and ports the sales director for exports, Marcel Modler, smiles and says: “Actually these grabs deserve the Blue Angel.”
Transfer point upgrades raise throughput, reduce dust
The largest independent terminal operator in North America has announced completion of a load-out hopper and four belt conveyors capable of carrying as much as 1,500tph (metric tonnes per hour) of mineral ore concentrate, complete with five transfer points that comply with the company’s ‘zero spill’ principle. The entire system of chutes and transfers at Kinder Morgan’s North Vancouver, BC facility was designed by Martin Engineering, custom-engineered and modelled in 3D.
The Martin Transfer Chutes confine the material stream and reduce air entrainment, while directing the moving material onto the receiving belt with minimal impact to reduce spillage, abrasion, dust and premature wear. This control also helps ensure that material is center-loaded on the belt, avoiding mis- tracking and fugitive dust. The new transfer points provide the dual benefits of minimizing aeration and preventing buildup within the chute, which is particularly important when dealing with combustible materials.
Four of the new transfer points employ a modular load zone transfer concept, with the discharge chute at the top of the system and a receiving chute to place material onto the belt being loaded. These engineered flow chutes employ special geometries that capture and concentrate the material stream as it travels through the chute. The fifth transfer point required a heavy-duty impact area at the bottom of a hopper to handle cargo from two front loaders.
Environmental Stewardship and Safety are among Kinder Morgan’s core principles, and all the minerals concentrate storage and handling facilities at the terminal are fully enclosed to ensure that no fugitive material escapes into the environment. “When we spent some time reviewing the existing transfer points, it became apparent that there was now better technology available, and we wanted equipment that could elevate the performance and containment to a new level,” said K-M Engineering & Project Development Manager Al Price-Stephens. During initial meetings, the Martin Engineering team introduced a variety of new technologies to improve efficiency and dust containment. “They helped us reach a good understanding of what’s available, and we found additional details on the company’s web site,” Price-Stephens continued. “We also became very familiar with the Martin Engineering book, Foundations IV, which has become the bible of bulk materials handling.”
To address the site’s specific requirements and design the optimum containment, Martin Engineering conducted a site survey, followed by a conveyor risk assessment. The strategy that emerged saw Martin Engineering take responsibility for the design and fabrication of the five transfers, as well as supervising the installation by an outside contractor.
“Load zones and discharge points are prime sources for the creation and release of airborne dust,” explained Martin Engineering global projects manager Greg Bierie. “The amount of dust created in a transfer point depends on a number of factors, including the nature of the material and the height of the drop onto the belt, as well as the speed and angle of the loading and unloading belts,” he said.
The project was kicked off with material testing at Martin Engineering’s Center for Innovation at the company’s headquarters in Neponset, IL. “By testing the customer’s specific bulk material and applying those properties as the initial step in chute design, we can develop a transfer that maximizes capacity, while minimizing the potential for build-up and fugitive material,” Bierie observed.
Weekly meetings were held from the beginning of the project through final design, which allowed all participants to see and discuss the status of each transfer point as it was being designed. “Martin engineering works with a 3D model, which not all designers do,” Price-Stephens said. “It’s much easier to look at a 3D model and resolve some of the potential issues before fabrication.”
“To some extent, I think bulk terminals like ours have learned to live with a certain amount of spillage and dust, believing that it’s unavoidable,” he added. “We’ve proven here that isn’t the case. When you look at the components and see what’s been designed for this facility, you realize that it’s really about simple things done well.”
Kinder Morgan is the largest independent terminal operator in North America, with 180 locations. The Vancouver Wharves terminal in North Vancouver, BC delivers inbound and outbound services to shippers moving cargo between all regions of western Canada, handling more than 600,000 metric tonnes of mineral concentrate per year across five different storage buildings.
Founded in 1944, Martin Engineering is a major player in making bulk materials handling cleaner, safer and more productive. The company supplies flow aids and conveyor products around the world for a wide variety of bulk material applications, including coal, cement/clinker, rock/aggregate, biomass, grain, pharmaceuticals, food and other materials. The firm is headquartered in Neponset, IL, offering manufacturing, sales and service from factory-owned business units in Brazil, China, France, Germany, Indonesia, Mexico, South Africa,Turkey, India and the UK, and under exclusive licence with ESS Australia.
Dustless loading with Cleveland Cascades Ltd’s award winning loading chutes
Having achieved awards for environmental engineering, environmental achievement and export achievement, there is no doubt that Cleveland Cascades Ltd is proficient in bulk loading solutions, using its unique cascade system.
Based in the UK, the company employs the original inventors of the cascade chute, together with a dedicated team of experts in design, manufacture, assembly and commissioning of bespoke loading chutes for the handling of dry bulk materials.
The unique Cleveland Cascade chute originated from an in-house project developed at a bulk handling facility on Teesside in the early 1990s. The facility had faced pressure from port operators and surrounding businesses relating to the safe and efficient loading of potash. “At the time we looked at the existing market for loading chutes but were unable to find a system to meet our requirements, so we put our heads together and designed our own,” says chairman Ian Barnard. The success of the system saw the idea patented and sold worldwide, handling a vast variety of dry bulk materials, from large lump iron ore and coal, to fine powders such as soda ash, phosphate and alumina.
The Cleveland Cascade system allows a controlled yet efficient transfer of materials from conveyor to ship, silo or stockpile. The material is loaded at a low velocity, yet high volume and this means products can be transferred with minimized generation of dust emissions and also minimized degradation and segregation of product. Such is the low environmental impact of the Cascade chute, Cleveland Cascades Ltd offers one of the lowest dust emissions for specific loading applications available from any manufacturer around the world.
With over 600 systems operating worldwide with applications in ship, silo, road, rail and tanker loading, the company’s key to success is its proven ability to provide a well- engineered solution with professional and committed support.
“Supplying projects to many of the world’s leading corporations, including ThyssenKrupp, FL Smidth, BHP and many more, each project delivered brings new challenges in terms of project specification, environmental issues, material handled performance criteria and increasingly dust emissions. Our approach is for our Commercial, Design and Engineering teams to work closely with our customer counterparts from project inception right through to project commissioning,” adds Barnard.
More recently, the Cascade Chute has been used to effectively handle biomass in large quantities of up to 2,000tph (tonnes per hour). The renewable energy source is particularly dusty and can be potentially explosive. By engineering the exact system to suit each customer’s requirements, Cleveland Cascades Ltd is fast becoming the solution to the industry’s biomass handling needs, reducing dust emissions, whilst maintaining the quality of the product.
Drawing on previous experience, the company is constantly bringing in new ideas, product development and expanding its product range. The patent pending VariFlow System is the second generation Cascade Chute, with the ability to automatically adjust cone inclination during loading to ensure absolute minimal dust emissions at all times, regardless of fluctuations in product feed rate. Similar in concept to the Cascade system, to optimize flow rate the VariFlow can operate in alternative modes. In standard mode, cone inclination is maintained at a fixed angle to suit the range of materials anticipated. In remote mode, the cone angles are adjusted to optimize flow rate for a particular material. In intelligent mode, sensors in the system monitor the material’s speed of descent and the cone angles are constantly adjusted to optimize the flow rate.Where materials are damp, dust free or slightly sticky, the VariFlow System can operate as a free-fall chute.
In addition the company has also developed and supplied Cascades Transfer Chutes to solve the dust emissions problem created at conveyor transfer points. This represents a logical step for the business, as for years it has provided the means for materials loading from the conveyor to receptor, ship, rail wagon or tanker etc. And so now it is providing materials loading in the same controlled manner between two conveyor belts.
The transfer chute combines existing cascade and materials flow technology, along with experience with innovative design and engineering solutions. The transfer chute is able to work between belts positioned at 90° to one another, inclined belts, and also height adjustable belts. Use of an outlet which presents material onto the belt in its natural profile, creates maintenance free and dust free delivery onto the belt.
While Cleveland Cascades Ltd actively promotes Cascade technology, a proportion of the business is for applications that do not require the stringent dust control and reduced degradation effects offered by the Cascade system.
To this end, design and manufacture is offered for a range of lower cost conventional telescopic chutes, together with a range of smaller chutes for truck, tanker and rail loading operations. These chutes are robustly constructed and well-engineered. Materials of construction are bespoke to the application and special requirements are catered for. The design is such that these products will give many years of trouble free service.
Cleveland Cascades Ltd remains at the forefront of innovative design within the bulk industry, taking its technology and experience, and tailoring it to meet the demands of individual customer needs.
Designing an efficient intake pit dedusting system with Bühler
The unloading of bulk materials such as cereals into intake pits is generally associated with considerable dust emissions, write Andreas Rembeck and Rico Hindemith, Bühler GmbH, Beilngries. The reasons for the need for an efficient receiving pit dust control system can be diverse. They range from reducing dust emissions in neighbouring residential areas to improving health and safety at work for those working on site and the imperative requirement of preventing serious damage to plant and danger of fatal injury from dust explosions.
Bühler Grain Logistics offers a choice between two systems, depending on application requirements: namely central or distributed receiving pit dust control. These can be further subdivided on the basis of whether extraction is above or below the grid iron. Both systems are of modular design and can therefore be customized to the specific conditions of each situation.
To ensure that the required aspiration capacity of the intake pit dedusting is kept to the minimum, every component needs to be optimized. It is therefore an advantage if there are gates at the entrance area which are kept closed at all times during unloading so that undesired air draughts and dust escaping to the surrounds can be prevented at the outset. For an optimum air flow inside the reception area, the upper section of the side wall is fitted with louvers. This prevents dust getting whirled up and ensures that the dust which collects is directed towards the extractors (Fig. 1).
Another technical step towards minimizing dust emissions can be taken by installing a dust barrier. The barrier has dust retention panels (Fig. 2) and prevents dust whirling up in the hopper. Practical experience from day-to-day operations has shown that up to 75% of the dust which is generated is produced when the bulk material hits the floor of the hopper. The dust barrier reduces air requirements, allows smaller filters and fans and cuts the power requirements of the fans by approx. 60%.
FILTERS FOR INTAKE PITS (DECENTRALIZED)
For operations such as grain collection facilities or farms where the amount of dust generated is insignificant or plays only a minor role at most, decentralized dedusting is the more appropriate solution (Fig. 1). In this case two adjustable inlet openings allow the air which requires cleaning to flow into the filter panels, from which it is directed to the fan through a manifold pipe line. The filter modules are connected together by connecting elements to form a single unit and the cleaned dust falls back into the reception pit via a diagonal plate.
CENTRALIZED INTAKE PIT DEDUSTING
Centralized dedusting is designed more for food processors such as grain mills and producers of pasta, where removing dust from the raw product is essential. As in decentralized dedusting, the air to be cleaned is also caught by an aspiration panel. The individual aspiration modules are screwed together, which means that a variety of intake hopper sizes can be created ranging from 4m to a maximum of 24m in length. The aspiration panel is connected to a dust manifold pipe line which leads to a Bühler round filter. The round filter is a central filter with a jet-pulse cleaning system. This is where the flow of raw gas which is picked up and the dust which is retained are separated. The dust is conveyed through dust discharge chutes to separate dust containers or big bags. As a result, the unwanted dust no longer comes into contact with the product, thereby ensuring improved hygiene and greater safety.This system could be described as a form of initial pre-cleaning.
FILTER
TA-Luft directive requirements under the German Federal Emissions Control Act stipulate emission limits of 20 milligrams of residual dust per normal cubic metre of air. The use of anti-static filter bags is one way of ensuring compliance with these reference values. They are more effective at cleaning than filter cells and also permit higher air to cloth ratios.
Cleaning is on a time-controlled or/and differential pressure controlled basis, which ensures optimum filter performance and saves energy.
COMPARISON
The two types of intake pit dedusting systems can be designed for both side and rear unloading. With their adjustable double gap they can be customized to local conditions and are capable of aspiring even if the intake pit is overfilled. Depending on requirements the walls can be supplied with filter modules only or with partition walls as well, enabling sizes ranging from 2×3m2 to 4×24m2.
The differences between the two filter systems are as follows: whereas the decentral dedusting system has a larger surface and therefore a lower filter load than the central dust removal system, the maximum dischargeable air rate of 55m3 per minute and meter of pit length with a filter load of 5m3 per minute and m2 of filter surface (grain) is less than the dischargeable air rate of the central solution, which is a maximum of 65m3 per minute and metre of pit length for the same filter load.
Separate dust separation in the central version means that the central version requires more space for Bühler round filters (Figure 4) and dust containers. On the other hand the decentralized dedusting system involves additional costs in terms of compressed air for cleaning the filter bags.
The purchase costs of the central receiving pit dedusting system are generally higher than for a decentralized system because the former has more components. In terms of operating costs, however, the central solution normally works out better. Both systems have their advantages. The decision as to whether preference should be given to the central or decentral option depends on the specific application.
Buttimer: designing for dust control
Buttimer Group has been designing port facilities and bulk handling equipment for more than three decades. From complete turnkey bulk terminals, to design and fabrication of bespoke shiploading and unloading equipment, the company has encountered many diverse bulk handling environments, developing comprehensive experience of dust suppression and environmental control techniques suited to each bulk product and port.
The requirements of environmental regulations placed on ports, the need to provide a safe and clean environment for port workers and those living in close proximity, and a greater awareness of fire safety and ATEX precautions relating to the dust from dry bulk materials has drawn an increased awareness of environmental control needs at port facilities. Buttimer has recognized this increased awareness and demand from customers and works closely with clients to provide optimized environmental controls for dry bulk handling systems, from turnkey terminals to mobile hoppers.
Many problems occur as a result of airborne dust. Firstly environmental; bulk cargoes range from feedstuffs, grains and cereals, fertilizers, coal, iron ore, biomass and others and each product has different health hazards and safety issues associated with it, these are further accentuated when the port area is in close proximity to residential or commercial buildings. Sea or water contamination can also be a concern. Secondly, the dust can cause havoc with mechanical equipment on the quay. Air filters and engines can become clogged and choked in short periods of time. Thirdly, cleaning of the surrounding areas can be time-consuming and expensive, not to mention hazardous.
DESIGNING A DUST CONTROL PROCESS
Buttimer has been designing and building mobile, rail and stationary dockside unloading hoppers for more than 20 years. During this time, numerous technical challenges have been encountered and solved — be they functional, structural or mechanical. In recent years, the demand for quicker cycle times of both unloading and loading of ships coupled with larger vessel sizes, has led to an ever increasing demand for larger capacity and throughput of handling equipment. This, however, brings with it its own problems; the larger the capacity means the larger the equipment, and so there are huge structural and mechanical demands — plus the rapid displacement of large quantities of dusty product creates explosion risks, mechanical problems and environmental hazards, as described.
As a direct consequence of the nature of crane and grab bulk unloading, large quantities of airborne dust are generated. The main areas where this occurs are where the grab releases the product into the hopper and where the product is then fed from the hopper into a truck or wagon or onto a conveyor. As the cargo is dropped into the hopper an equivalent quantity of air is displaced and as it evacuates the hopper it brings dust with it. Then, as the product is released into open wagons and trucks, the effect is repeated.
When Buttimer developed its unloading hoppers, DMLs (Dockside Mobile Loaders), RMLs (Rail-Mounted Loaders) and SMLs (Static Mounted Loaders), it endeavoured to address dust emitted in the loading and unloading of the hopper. Firstly, fitted on top of the hopper, is the loading thimble. This is an approximately 3m-high wall above the top of the hopper into which area the grab is situated before opening and discharging the product. Secondly below the thimble and directly on top of the hopper there is a thrash grid to stop any unwanted objects or lumps of product. This thrash grid is sitting on a flexible flap system. This is a simple mechanical system that has angle steel plates with vertically hanging rubber flaps. Finally the thimble sits flush with two sides of the hopper and on the other two sides it sits inside the hopper wall. Within this cavity are placed insertable reverse jet cassette filters.
A brief description will demonstrate how this system creates effective dust containment in Buttimer’s unloading hopper units. As the grab passes into the thimble opening and starts to discharge it creates an enclosed finite space bounded by the open grab on top, hopper at bottom and thimble on all four sides. As the cargo passes through the flexible flap system the flaps move to the side, the cargo slides over the angled plates and the rubber flaps close after stopping the dust passing back up through the grid as the air is displaced. However, approximately 10% of the grid is left open, to allow for the intake of air so that the reverse jet filters have the required quantity of air to pull. The reverse jet filters suck the dusty air from the thimble area through the cavity between the thimble and hopper sides. The reverse jet system then clears the filter bags and the dust then falls directly into the hopper.
In the unloading area there are installed hanging rubber curtains that the wagon or truck can drive through, again creating a controllable and finite space beneath the hopper — limiting the effects of wind or environment on dust at the release point. Also situated on all hopper outlets are mechanically operated loading chutes, which are fitted with an automatic retraction system so that the cargo will drop the minimum distance to the bed of the truck or wagon and hence generate as little dust as possible. There is a fan connected to the chutes which extracts dust up through it and is in turn blown back into the top of the hopper. Where a conveyor is the means for evacuating the product the connection between it and the hopper is easily controllable and so doesn’t cause extra problems.
PROTECTING EQUIPMENT
A common problem that Buttimer has identified with many mobile unloading hoppers on the market is that the generator, compressor and mechanical drives become choked with dust and over-heat. To solve this problem a dust-free control room has been situated in the mid-section of Buttimer’s DML hoppers. This room is kept dust free by maintaining a high positive air pressure in the room and hence the dust is not drawn in. This is achieved by installing a fan system to blow the required volume of filtered air into the room. This also has the added benefit of keeping all running motors cool during operation in high temperatures.
Buttimer’s equipment is designed for longevity and efficiency; using the flexible flap system described reduces the quantity of air that needs to be pulled through the cassette filters in the hopper’s thimble by more than 60%, compared to having an open grid. This saves greatly on operating costs and substantially limits the dust emitted into the environment. The units are easily cleaned between use or bulk products by means of an onboard hose reel system accessible to all areas of the unit for flushing down. This is part of ensuring that Buttimer’s units are able to cater for multiple products, easing or eliminating the fear of cross contamination.
Buttimer also designs and installs complete turnkey port terminals, where attention to environmental controls for individual units is compounded by a systematic attention to dust monitoring and safety concerns in the design, process engineering, procurement and installation project phases of a dry bulk port terminal. Bulk products such as animal feeds, oilseeds meal and types of biomass can be particularly flammable. Buttimer assigns ATEX fire safety codes both internal and external to all relevant equipment, including investigation of the ignition point. Where pertinent, equipment is fitted with special spark prevention features such as plastic casings on bucket elevators, anti-static rubber on drums, rollers and other high friction points, as well as using anti-static belts on conveying equipment. Assigning ATEX ratings, predicting dust levels in and around equipment, identifying transfer points and potential fire hazards are integral to Buttimer’s process design. When dealing with a product like soybean meal or types of biomass, it is essential that the system be tailored to the product’s characteristics; ‘off-the-shelf ’ handling solutions will be ineffective and often unsafe.
OPERATIONS MATTER AS MUCH AS DESIGN
Buttimer emphasizes that the design innovations and precautions mentioned will reduce and limit the dust emitted but cannot completely eliminate it. Due to the nature of the products handled and the fact the grab is open to the elements from ship to unloading hopper one can never claim to eradicate dust altogether. Also the effectiveness of the system is very much dependant on the competency of the crane and unit operators. Buttimer have supplied turnkey port solutions, as well as DML, RML and SML units to many different clients in numerous countries and for a broad spectrum of bulk products and have received very positive feedback — more convincingly, nearly 80% of Buttimer’s business is repeat customers.
Freight handlers flatten dust at Ukraine port terminal
The largest private stevedoring company in the Ukraine has significantly improved air quality and reduced dust-related complaints at the country’s deepest port, a busy marine terminal where ocean-going vessels have 24/7 access to services. The key is a mobile dust suppressor designed to produce massive numbers of tiny water droplets that are specifically sized to attract dust particles. Launching an atomized mist with a powerful oscillating fan, one oscillating unit is able to cover 125,000ft2 (11,613m2) from a single location, an area more than two-and-a-half times the size of an American football field.
Situated on the Black Sea at Adzhalik Bay, about 24 km south from the city of Odessa, TIS (TransInvestService Ltd.) specializes in transshipment of coal, grain and fertilizers in bulk quantities. With the opening of its new coal handling berth at the end of 2008 — and a terminal that has the estimated capacity to move 10 million metric tonnes per year — the facility greatly increased its already significant potential for dust.
“With the ability to handle such large quantities of dust-generating materials, we felt that some form of suppression had become a necessary element of port management,” observed Alexey Shlapakov from TIS. “We have specialized equipment for many of our operations, and we started doing some research on the available technologies for dust control. After comparing features and benefits, we specified a DustBoss® model DB-60,” he said.
The DB-60 is one of the largest designs in the product family from Dust Control Technology (Peoria, IL), a specialist in this growing niche industry. The firm currently provides a number of electric models, hydraulically-powered units, tower-mounted designs and remote controls, as well as many other dust-related components.
“Dust and odour management is becoming more critical all the time,” commented the company’s CEO, Edwin Peterson. “What used to be considered an option a few years ago is now frequently a mandatory component of project planning,” he said. “Tighter regulations and greater environmental awareness are both contributing to that trend.”
THE FACILITY
The port has an average depth of about 14 metres and a quay wall that is more than 1,000 metres long. It features two shiploaders capable of handling 950 tonnes per hour and a portal crane with a lift capacity of 16 tonnes.
Situated on 500 hectares of land, the TIS facility has a loading capacity of up to 25,000 metric tonnes of coal per day, with warehouse storage for about 270,000 tonnes. It can also handle as much as 35,000 metric tonnes of grain per day, with warehouse storage for approximately 380,000 tonnes, and is equipped to load up to 25,000 metric tonnes of fertilizers per day, with warehouse space for about 270,000 tonnes. Company officials estimate that as many as 1,000 trucks can be loaded in a single day, or up to 250 railway cars.
With that kind of capacity,TIS needed a dust control solution to match. The DB-60 is built around a powerful 25 HP motor that generates 30,000 CFM. It features 30 brass nozzles developed to atomize droplets to the optimum size for dust suppression — between 50 and 200 microns — and can be customized to suit specific particle sizes and operating conditions. The high-performance design includes an optional booster pump that delivers up to 200 PSI of pressure from a supply hose.
“We noticed the effects of the DB-60 right away,” Shlapakov continued. “The air quality was noticeably improved, with a definite reduction in fine airborne particles. We soon found that dust-related complaints had also dropped. The unit has proven its value in service, under some very difficult conditions, and has met all of our expectations.”
TIS is the Ukraine’s largest private stevedoring company, located at the nation’s deepest freight harbour. Situated on Adzhalik Bay, which never freezes, even the largest ocean vessels have unrestricted access to services around the clock. The firm is equipped with grab loaders, 11km of conveyors and other specialized equipment, earning it a reputation for rapid turnaround times.
Dust Control Technology is a leader in effective dust management solutions for bulk material handling, serving in port/shipping applications, coal power, demolition, recycling, composting facilities, mining operations and scrap industries. The company’s DustBoss® product line has been supplied to customers in 40 different countries to date, helping reduce labour costs and free up manpower for more important tasks.
The automated units also use less water than hoses and sprinklers, with some customers realizing payback in less than six months and netting an annual cost savings of more than $50,000.
Dust control systems: TMSA — a South American expert
Each time products are elevated, transferred or handled, generate dust in high-volume, causing prejudice to the health of operators and damage to equipment, and might still cause fires and explosions, depending on its excellent combustion capacity. Dust control is a significant means of preventing explosions in grain storage units and reduces environmental contamination. The separation of the dust of the dust/air mixture is a process that requires a lot of care.
Dusts are particles with a diameter size between 1 to 100 microns, each particle type and composition influences its explosive risk. A concentration greater than 30gr/m3 shows explosion risk, with dust of less than 60 microns, this situation is illustrated as an appearance of a mist or haze. Some products generate more dust than others, while being conveyed.
Environmental management and pollution control pose major concern to all sectors of mining, steel, power, cement, agro- commodities and other core industries.
Dust can be explosive and the explosiveness of dust depends on multiple factors. In order to assure that an explosion is not produced, the equation ‘dust + oxygen + ignition’ must be altered. The elimination of any one of these requirements will prevent the reaction. This can be done by neutralizing ignition sources or eliminating or reducing the emissions of dust. Dust is eliminated by controlling its generation or installing vacuum systems that collect the dust in filter bags at each point of emission. With the increase in awareness of the problems related to pollution, a challenge has arisen to solve and control the spread of air pollution. Strict environmental regulations as well as the sensitivity with respect to air pollution has motivated TMSA Tecnologia em Movimentação SA, from Brazil, to adopt new approaches in engineering with an emphasis also on waste reduction for controlling the air borne dust emitted due to transport, transfer, storage and distribution of bulk materials.
DUST CONTROL TECHNOLOGY IS NO LONGER AN OPTION BUT A REQUIREMENT – THIS IS HOW TMSA UNDERSTANDS THIS ISSUE
Energy efficiency, work safety and reliability are no longer a wish list for dust control systems.
To reduce dust emissions to the environment, to minimize explosions and fire risks,TMSA installs de-dusting systems at the emission source where the dust is aspirated, collected and treated or is controlled with very low or negligible emissions, maintaining the dust in the product flow. It contributes to reduce maintenance costs, preserve cleaner environments which improve health care, operational efficiency, and good neighbour relations.
Conveyor design also plays an important role in dust control. TMSA, as a strong conveyor specialist, reduces dust emission with special engineering and careful manufacturing, by:
- conveyor designs with low belt speed/control of air flows/ eliminating bumps between idlers/covered conveyors/good chute designs/minimizing transfer points;
- use of enclosed conveyors: screws, redlers, special designed belt conveyors as Manutubes (belt conveyor inside a plastic tube) and pipe conveyors;
- tight bucket elevators with good boot and head designs with no back legging and moderate belt speeds;
- avoiding long chutes with high angles and installing speed reducers; and
- avoiding dust accumulations and dust turbulences inside conveyors.
DUST CONTROL SYSTEMS
TMSA offers different tools to control the dust: conventional with aspiration/innovative with no aspiration.
For any type of dust suppression system the principle is to suppress the dust at the source and thereby preventing to be air borne. Dust suppression systems are tailor made depending upon the application and behaviour of the dust generation and requires equipment sizing and selection considerations for capturing, conveying and collecting, plus hood and ductwork design options, system balancing and testing, fans or pulse-jet or compressors and exhaust stacks. TMSA’s dust collection systems are engineered to each application. When it comes to selecting equipment to manage air quality you need a number of alternatives that can achieve the desired result. With nearly 50 years of experience and state- of-the-art capabilities,TMSA can meet and exceed any project needs.
TMSA offers a complete range of bag houses: high pressure, medium pressure, low pressure filters, with bag cleaning by fans, compressed air (jet-pulse) or Roots type pumps.
Styles ranging from round, square, vertical, horizontal with bottom loading filters and top loading filters plus a variety of inlet configurations, its engineering uses different types of fabric filter dust collectors with a focus on pulse-jet cleaning technology. In addition to the standard units,TMSA can manufacture special units, design centralized de-dusting systems with big central filters collecting from different sources or compact filters which collect dust in each source and returns the dust to the product flow.
The compact filters are an alternative to centralized aspiration systems, ideal to install on silos, transfer chutes, scales, ship loaders or individual conveyors and machines. The big advantage is their reduced size, low energy and that the collected dust is discharged directly on the dust generation point, continuing the product flow and making unnecessary the installation of dust containers and long collection tubes.
DUST CONTROL SYSTEMS FOR TRUCK OR WAGON RECEPTION PITS
Most materials, such as grain and other granular materials produce dust or have dust associated with them and the dust rises from the bottom of the pit in large quantities when a load of grain or granular material is dumped into the pit which may be 5 to 8 metres in depth.
This dust cloud is formed by the granular material hitting the bottom of the pit; the force of the material loosens the dust and also forces the air upwardly as the air in the pit is replaced by the solid material. TMSA offers solutions related to hopper assemblies for receiving from a wagon or truck granular and/or grains dumped into a pit for storage or removal from the base of the pit while controlling and containing the dust during dumping. Its ‘vacuum systems’ have gravity baffles that pivot with the weight of the falling material. When unloading in the intake pit the system only opens in the spot where the product falls into the pit while the remaining pit area stays closed. At the same time, the generated dust quantity is collected and sucked down through the pit by means of a fan upon which the dust is separated through a filter. )
The ‘DustMaster System’ provides the unique method of controlling the emission dust from a pit into which granular or grains are being dumped, with no aspiration. Control of the dust is provided by the use of controlled metering sections and dumping sections which constitute a part of the cover for the pit.
The DustMaster provides for rapid unloading of grain or granular materials into a pit while preventing the dust generated thereby being carried by the air in the pit from escaping into the atmosphere. Offers a cleaner work environment; direct payback comes in the form of lower cost installation, energy savings and savings from the reduced shrinkage.
DUST CONTROL FOR LOADING TRUCKS, WAGONS, SILOS
TMSA uses conventional solutions for loading trucks, wagons or vessels as retractable or telescopic loading spouts, and has also developed and patented a special dust control system for loading vessels: the ‘Dust Trap’ and has incorporated the DSH-Dust Suppression Hopper from New Zealand.
The shiploader usually has dust collecting points both in the belt conveyor admission area and in the discharge of the moveable head chute inside the boom. High efficiency circulator fans, cyclones and compact filters handle the dust generated during the ship loading. Collecting points are installed surrounding the areas where the dust could be generated in the belt conveyor admission. A square pipe is installed on the both sides far front of the boom at the head chute discharging area. A moveable car to collect the dust runs inside these sealed pipes back and forth over the full length of the stroke, attached to the head chute. The back portion of the boom will have a pipe also in both sides to carry the dust to the cyclone and filter.
TMSA has developed a system for dust suppression and trimming (combined): the ‘Dust Trap’.
It reduces the dust emissions by straitening the space for product to go through the pipe, controlled by a PID circuit and sensors, makes the product itself to act like a seal against dust releasing, without strangulating its flow. It accumulates and compacts the product flow to a minimum, which reduces the dispersed amount of air in the interstitial space. It prevents the air/dust from escaping from the telescopic duct. It can be adapted for existing shiploaders.
Recently the DSH-Dust Suppression Hopper, from New Zealand, has been incorporated, with great success, having interesting and successful applications in Argentina and Brazil. The DSH system requires no air, no hydraulics nor electricity. There is no waste dust stream to handle and TMSA’s load out rate was not affected at all.
This dust-free loading spout ingeniously contains the dust within the product stream when discharging dry bulk materials.
Thus, it cleverly avoids the need for the more complicated retractable or telescopic loading spouts that are more commonly used in today’s truck loading and out-loading applications. Easily installed, the DSH Systems hopper eliminates dust and reduce hazards, health risks and wastage.
TMSA Tecnologia em Movimentação S/A, is one of the big suppliers in the South American market for bulk solids material handling, especially in port terminals and heavy duty and long distance conveyors, together with its dust control systems.
Based in Brazil,TMSA Tecnologia em Movimentação SA’s head office is located in Porto Alegre, Rio Grande do Sul State, where the company has an important manufacturing shop of 32,000m2 with large and highly integrated engineering capabilities, with in house mechanical, civil, structural, electrical, automation and de-dusting specialists; all under ISO 9001:2000 Certification.
The working team is composed by approximately 500 employees including their branch offices in Belo Horizonte and Bulktech Argentina SA in Buenos Aires. There is a large team of over 50 multi-aged engineers and designers that guarantee a ‘state-of-the- art’ solution today and long-term support with in-house mechanical, structural, finite element analysis, electrical, automation and dust control specialists.