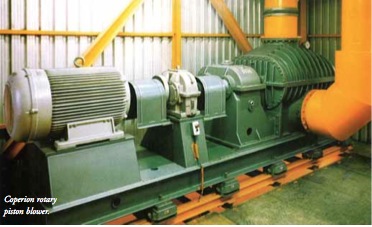
What should a state-of-the-art vacuum ship unloader look like?
Coperion is a leading supplier of pneumatic vacuum ship unloaders for the unloading of alumina and petcoke from seagoing vessels. In 2007, the company Hartmann — which has over 100 years of experience in the field of pneumatic ship unloading — was incorporated into Coperion.
Coperion’s vacuum ship unloader’s design can be adapted to suit the climatic conditions of the site where it will operate. Designed unloading capacity ranges from 150tph (tonnes per hour) to 1,200tph.
SINGLE OR DOUBLE BOOM
The distinctive attribute of a vacuum ship unloader is the number of unloading nozzles and conveying pipes. Usually, there are one or two pipes, with each arranged on a boom — there are therefore single- or double-boom unloaders.
A single-boom design has its advantages; it requires a minimum amount of equipment and a lighter steel structure, due to one single point for the introduction of power. The less equipment that is required, the lower amount of maintenance is needed — therefore the maintenance costs for a single-boom design are lower than those for a double-boom design. The double-boom design is more flexible, and unloading can be carried out from two separate hatches. Another big advantage is the high availability of the system, due to the fact that unloading can continue with one boom if there is a technical fault with the other one. Also, the resting process is faster with a double-boom design and reduces the berthing costs of the ship.
CONVEYING LINE
The conveying line of the vacuum ship unloader has various special pieces of equipment, which are described below.
To ensure the smooth conveying of the cargo, it is necessary to adjust the product fluidization and the conveying air at the product pick-up point. Coperion has designed a special suction nozzle with adjustable setpoints for the false air, i.e. the air that will be aspirated in addition to the mixture of bulk material and air at the nozzle inlet. This leads to an optimized, stable and safe aspiration process at the nozzle inlet, resulting in a stable and reliable pneumatic conveying process in the pipe.
The telescopic vertical suction pipe is needed to reduce the lifting height during the lifting of the boom and to adapt the pipe length to the tide height of the ship.
After the vertical suction pipe, the 90° bend is needed to guide the product flow. On this 90° bend, the product flow impacts directly and wears the lining of the bend. To ensure a long life, these bends are lined with basalt or ceramic. Another important feature after the 90° bend is a pipe extension with the same lining like the 90° bend to reduce the wear of the first part of the horizontal suction pipe where the product stream is still a strand on the pipe top.
The horizontal pipe can be either fixed or telescopic. Whereas the fixed pipe has lower and maintenance investment costs, the movable pipe is more flexible to position the vertical suction pipe in the hatch. Without a telescopic device at the horizontal pipe, often the entire ship unloader has to be moved to place the suction nozzle in the desired position.
A highly efficient pre-separation of the bulk material from the conveying air is necessary in order to protect the filter bags of the vacuum filter, and to extend the lifetime of the latter. Therefore Coperion has designed a filter with a pre- separation of bulk material and air. As a result, Coperion can optionally use filter cartridges instead of filter bags, with the result that the filter housing can be downsized. The Coperion filter specialists are continuously working to improve the performance of the filter and to give its customers state-of-the-art technology or to update the existing filters.
Coperion has two different systems for the airlock beneath the filter. Both airlocks are based on the rotary valve design, which assures continuous discharge. The first air lock system is the Coperion rotary belt discharger. This solution is a well proven and economically interesting technology.
The second solution is the Coperion ceramic-lined rotary valve. This solution has a very long life, and helps keep maintenance costs low.
For discharging the product from the rotary valve to the jetty conveyor Coperion offers different solutions depending on the bulk material. These solutions are:
- Coperion Duroslide (air gravity conveyor), only for alumina
- belt conveyor
- through chain conveyor
To generate the vacuum in the conveying system, Coperion uses its own rotary piston blower or a fan. Each of the two principles has its advantages in different application sizes.
Two-stage fans will normally be used in vacuum ship unloaders with high capacities (>300tph) in one conveying line. Fans have the advantage of low investment costs.
Below a conveying capacity of 300tph, the rotary piston blower has proven to be the best technical and economical solution.
STEEL STRUCTURE
Beside the process equipment in the pneumatic conveying line, there are different mechanical aspects that make a Coperion vacuum ship unloader unique.
The slewing mechanism for the boom can be located directly below the booms, so only the boom slews. Another solution is to locate the slewing mechanism under the filter housing; that means the entire upper part of the unloader — including all equipment like filter, rotary valve and the rotary piston blower/fan — move with the boom.
Only with the choice of the best steel structure concept and the application of modern FEM design techniques can the most convenient solution for the steel structure be provided.
MODERNIZATION, REFURBISHMENT
Beside new vacuum ship unloaders, Coperion is also carrying out engineering studies and revamping projects of vacuum ship unloaders, for example on the following items: v exchange of the bogies;
- boom exchange;
- filter refurbishment;
- exchange of the control system; and
- throughput increase.
SUMMARY
Before designing and installing a new ship unloader, many different parameters have to be considered. These range from the environmental data (temperature, wind forces, earthquake forces) to the individual requirements of the customer (maximum loads on the jetty, unloading capacity, resting process). As shown above, there are many technical solutions available for each part of the pneumatic unloading process, for the supporting steel structure and for the motion of the ship unloader. Only with the specialized expertise from an experienced company such as Coperion, which has access to the whole range of technologies for each part of the process, is it possible to design the optimum technical and economical solution that fulfils the project and customer specific requirements.