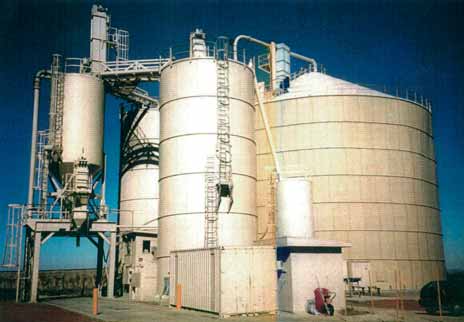
Jenike & Johanson is active in powder and bulk solids handling, processing, and storage technology. Over the past 55 years, the company has tested over 10,000 unique powders and bulk solids and worked on more than 7,500 projects, giving its team the broadest real-world and in-depth experience in the industry to address a wide variety of bulk material handling and engineering needs.
Jenike & Johanson aims to help its clients improve the efficiency, reliability, and safety of their operations by preventing, eliminating, or reducing problems related to bulk material flow, storage, conveying, or processing.
The company offers a wide range of services, including investigating silo or equipment failures. Hundreds of industrial and farm silos, bins and hoppers experience some degree of failure each year due to improper design, faulty construction, and/or erratic operation.
Although failure may involve a catastrophic collapse of the structure, it can also display in less obvious forms, such as cracks in a concrete wall, wrinkles/dents in a steel shell, and/or bending/deflection of a support beam. Even these more ‘minor’ issues can be important danger signals, indicating that corrective measures are probably required.
Common equipment failures can involve:
- silos,bins,hoppers;
- feeders,conveyors,chutes;
- corrosion,erosion;
- reactors or pressure vessels;
- dryers or coolers; and
- silo inserts, supports, nozzles.
WHY IS EQUIPMENT FAILURE A PROBLEM?
Silo or equipment failures can be costly in many ways. Failures often contribute to:
- complete unit shutdown;
- increased labour costs;
- personnel safety risks;
- reduced production rate;
- unscheduled maintenance;
- litigation or liability;
- poor process availability; and
- environmental hazards
Jenike & Johanson offers great expertise in preventing and diagnosing equipment failures. Its team of experienced engineers have the required experience, on-site investigative skills, and state-of-the-art tools needed for these complex applications. How the bulk material interacts with the equipment is an important part of the investigation, and it offers a high level of expertise in material testing and physical and analytical modelling.
INVESTIGATION OF SILO OR EQUIPMENT FAILURES Hundreds of silos, bins and hoppers used in a wide variety of industries experience some degree of failure each year. In fact, these structures fail with a frequency that is much higher than almost any other industrial equipment.
Common failures
- catastrophic collapse of silo, bunker, or hopper;
- buckling, bending, denting of steel or aluminium silo wall;
- vertical or horizontal cracking, spalling, or delamination of concrete silo wall;
- damage to bin due to gas over-pressurization or vacuum (suction) effects;
- wall thickness loss due to corrosion or abrasive wear effects; and
- failure of screw feeder or reclaimer in flat-bottomed silo.
These failures are all important danger signals, indicating that corrective measures are probably required. The economic cost of a silo failure is never small. The owner faces the immediate costs of lost production and repairs, personnel in the vicinity are exposed to significant danger, and the designer and builder face possible litigation because of their liability exposure.
Project examples
- severe cracking in two of the largest reinforced concrete coal silos in South America through which 100% of the plant’s production is exported;
- massive thumping of a 10,000-tonne-capacity steel silo filled with fine sand at a high throughput LCD glass plant;
- extensive cracking in several large, inter-connected reinforced concrete grain silos at ethanol plants soon after being put into operation;
- failure of an 800-tonne-capacity, multi-compartment welded steel bin that shut down production at a concrete products plant;
- failure of a 1,200-tonne-capacity steel bin storing stone at a quarry that resulted in the death of several workers;
- screw feeder and rotary plow failures at a sewage treatment plant; and
- complete collapse of a 9,000-tonne-capacity bolted steel silo storing fly ash the first time it was filled with hot material (see below).
CASE STUDY
Because of its expertise and, Jenike & Johanson was called in to discover the reason behind the collapse of a silo used to store fly ash.
A new bolted steel storing 9,000 tonnes of fly ash from the adjacent coal fired power generation station split apart two
weeks after it was first filled to capacity. Up to this point, no ash had ever been discharged. Curiously, the silo collapse occurred at night when the silo was being neither filled nor emptied.
During the investigation into this failure, calculations showed that the silo was underdesigned and did not identify or account for a phenomenon called ‘thermal ratcheting’. The walls of outdoor metal silos expand during the day and contract at night as the temperature drops. If there is no discharge taking place and the material inside the silo is free flowing, it will settle as the silo expands. However, the material cannot be pushed back up when the silo walls contract, so it resists the contraction, which causes increased tensile stresses in the wall. The effect is repeated each day that the material sits at rest.
Also revealed were some cost-cutting measures taken by the silo supplier during the construction of the silo that contributed to the failure. The design specified that bolts of a particular classification, size and strength be used in the construction. These specified bolts have a distinct marking on their head that identifies them as having been tested and meeting recognized standards. Less than 1% of the bolts that were recovered from the failed fly ash silo had the specified marking and none of the marked bolts had been used in the critical vertical seams. Strength tests on the unmarked bolts revealed that some had tensile strengths less than the specified minimum.
The result
There were many contributing factors to the collapse that acted together, and if any one had not been present, the collapse of the silo might have been avoided. If proper bolts had been purchased and used, the silo collapse may have been avoided. If the silo had been inspected by an independent silo expert, either during the construction or after construction was complete, perhaps the incorrect bolts would have been noticed and corrective action could have been taken. Had the operation of the silo been such that material was discharged more frequently, the condition of accumulated stresses that precipitated the collapse could have been prevented.
The life of a silo can be divided into three distinct phases: design; construction; and utilization. In each of these phases there are numerous opportunities for errors that can result in structural failure. As in the fly ash silo failure described above, the majority of structural failures of bins and silos can be attributed to a combination of several deficiencies or errors.