The inland transportation of cargo by barge and rail offers many advantages, not the least of which is the much-reduced impact on the environment, a factor that is of growing importance in today’s market where environmental protection measures and regulations are ever more stringent.
According to the Inland Rivers Ports and Terminals (IRPT) association (the trade association for the US’s inland waterway, port and terminal professionals), inland barges carry approximately 15% of the US’s freight at the lowest unit cost while offering an environmentally-sound alternative to truck and rail transportation.
The IRPT estimates that one gallon of fuel enables one tonne of cargo to be carried the following distances:
- by truck: 59 miles
- by rail: 202 miles
- by barge: 514 miles
The measure of energy efficiency in transportation is the amount of energy used for the service provided, and can be expressed as the number of BTUs required to move one tonne of cargo one mile (a tonne-mile). In studies comparing rail, truck, and water, shallow-draught water transportation has been proven to be the most energy efficient method of freight transportation for moving bulk raw materials.
An analysis of rail and waterway fuel efficiency shows the average BTUs expended per tonne-mile totals 433 for water transport, and 696 for rail transport. It is much more efficient to move cargo through water than over land.
Size is the key to water transport’s efficiency.The capacity (1,500 tonnes) of an inland barge, which can carry five times its own weight, is impressive, and the industry as a whole has enormous capacity. The cargo capacity of a barge is 15 times greater than one rail car and 60 times greater than one semi trailer. To move the same amount of cargo transported by a standard tow (15 barges) would require a freight train two-and- three-quarter miles long or a line of trucks stretching more than 35 miles. On the lower Mississippi, one 10,000 horsepower
towboat can push 40 barges that have the carrying capacity of 600 railcars or more than 2,200 trucks.
CARGO CAPACITIES
Barge Rail Truck1,500 tonnes 100 tonnes 25 tonnes
52,500 bushels 3,500 bushels 875 bushels
453,600 gallons 30,240 gallons 7,560 gallons
Barge transportation is a low-energy form of transportation, and shifts of traffic to high-energy forms would be inconsistent with energy conservation efforts. The environmental advantages of water transport should be weighed when considering any activity that would result in a shift of cargo from the waterways to a land form of transport.
SAFETY
Transporting cargo safely is an important measure of environmental responsibility, and water transport has the fewest number of accidents, fatalities, and injuries as compared to truck or rail.
Shallow-draught water transportation has definite advantages over competitive modes: it generally involves less urban exposure than either truck or rail; operates on a system that has few crossing junctures; and is relatively remote from population centers, all factors that reduce both the number and impact of waterway incidents.
Truck and rail tank car spills occur more often than barge spills. Barges, because of their much larger capacity, require far fewer units than either rail or truck to move an equivalent amount of cargo, and so the chance of a spill is less likely. Also, design features of barges such as double-hulls and navigational aids help reduce accident frequency. Recent legislation requires all new inland tank barges carrying liquid cargoes to be built with both an inner and outer hull. However, for some time water transport operators have realized the need to protect the environment, and about two thirds of the inland tank barges that have been constructed in the last ten years have either a complete double hull, double sides, or a double bottom.
For any hazardous liquid material shipped by water, the United States Coast Guard maintains a comprehensive list of safeguards and controls that govern the design and construction of vessels and equipment, and personnel manning qualifications. Construction of tank barges must be approved by the Coast Guard, and once in service, they are inspected annually. Coast Guard statistics show that water transportation is better inspected and regulated from a safety point of view than either of its competing forms of transportation.
AVOIDING CONGESTIONThe steady increase in highway traffic in the US — and elsewhere in the world — has far outstripped any increase in infrastructure capacity, resulting in delays, safety problems, and congestion. In the US, this costs up to $100 billion annually.
Other impacts of traffic congestion are: accidents, increased energy consumption, environmental damage, increased commuting times, and greater social tension. Water transport, in contrast, does not have congestion problems, and seldom causes them for others. The fact is, that far from being congested, the US’s water transport system is under utilized.
PRODUCES LITTLE AIR/NOISE POLLUTIONSome of the most pervasive and intrusive sources of noise and air pollution are transportation systems.
Noise levels, with road traffic the chief offender, have been rising. Air pollution comes from a wide variety of man-made and natural sources, with fossil fuel combustion the largest contributor. Air pollution caused by transportation includes pollutants directly emitted by engines as well as secondary pollutants formed by chemical reactions. Road traffic is, by far, the greatest source of air emissions.
Water transport, conversely, causes far less air pollution than trucking, and less or comparable amounts, than rail. Cumulatively, it has a relatively minor effect on air quality, consumes much less energy (and as a result, produces less air pollution) per tonne-mile of freight carried than either rail or truck. For the most part, waterway operations are conducted away from population centres, which reduce the impact of its exhaust emissions. Little data exists on noise levels of barge operations, mainly because they are not considered a problem. Towboats operate well away from shore, with the sound of their engines muffled below the water line, and any noise levels are hardly audible beyond the immediate area of the tow.
HAS MINIMAL LAND/USE SOCIAL IMPACTTrains rumble through cities and trucks travel streets and highways. Barges, on the other hand, quietly make their way along isolated waterways.
Reduced social interaction, reduced access to other neighbourhoods, and increased traffic congestion and/or unwelcome traffic patterns are often a result of increased surface traffic.
The impact of rail lines passing through urban areas, and trucking operations occurring in close proximity to high-density population areas, can become a disturbing element to an otherwise reasonably calm environment in settled areas. By contrast, water transport has little impact on densely populated areas: shallow-draught vessels operate in mid-river, well away from shore, and because of the large tonnage moved at one time, tow passages are infrequent.
Since most of the right-of-way for water transport is provided by nature, navigation is less likely than other transport forms to compete with non-transportation uses for land area, an important consideration in urban locations. Extensive land area can be taken up by new highways and railroad corridors, but apart from a few connections and waterside terminals, waterways preempt very little land.
PRODUCES MULTIPLE BENEFITSTransporting bulk commodities by water has many other positive benefits and many beneficiaries.
When a new navigation project is completed, more than water transportation benefits. The other major beneficiaries of developed waterway systems include recreation, flood control, public water supply, irrigation, and industrial use, all uses that can be as important as the navigation project itself. Navigation not only creates opportunities for new industries, but may also change trade patterns that can have a major economic impact on local and regional development.
CONCLUSIONThere is a growing national commitment to restoring and preserving the environment, and this goal has become a priority in business planning.
The companies that make up the barge and towing industry have a reputation for a strong environmental stewardship and are dedicated to improving the compatibility of their operations with the environment in an effort to reduce environmental incidents to an absolute minimum. Pollution control, protection and enhancement of the environment, and maintenance of the ecological balance have long been major concerns of the waterway industry.
Moving freight by rail: a green alternative to trucking
Rail freight can contribute to the countries’ carbon reduction targets. In the UK for example: y freight moved by rail produces 70% less carbon than freight moved by road;
- rail offers the opportunity to save 4.6mt (million tonnes) of CO2 per year by 2030;
- longer trains will increase CO2 savings further;
- keeping freight trains moving would reduce CO2 emissions further; and the rail freight industry has many initiatives to reduce CO2 further
Action is needed to reduce the amount of carbon in the atmosphere to prevent the consequences of global warning. Sir Nicholas Stern, who published a report on behalf of the UK government in the autumn of 2007 stated that “Governments, businesses and individuals all need to work together to respond to the challenge. Strong, deliberate policy changes by governments are essential to motivate change. But the task is urgent”.
ENERGY EFFICIENCYNot only does using more rail freight reduce CO2 emissions but it is also more energy efficient. In these times of increasingly insecure and volatile oil supplies switching to transport modes which use less fuel will become vital to secure the future of the economies around the world.
MOVING TO A LOW CARBON ECONOMYThe UK, for example, is committed in statute to an 80% reduction in carbon emissions by 2050, and reductions are therefore necessary across all sectors. Government data shows that transport represents around 23% of UK domestic CO
2 emissions and within that, freight transport contributes just over 30%, which comes almost entirely from road freight.
On average, rail freight produces 3.4 times less CO2 per tonne-km than road transport. This means if a movement of goods switches to rail freight there will be a 70% reduction in CO2 emissions compared with the equivalent road journey. Encouraging modal shift from road to rail is therefore an easy way to secure significant reductions in transport carbon emissions.
MORE TRAINS MEANS MORE CARBON SAVEDCurrent rail freight in the UK is estimated to save around 6.7m lorry journeys per year, saving around 2.3mt of CO
2. With rail freight volumes set to double by 2030 the carbon savings will multiply and could be even greater with rail efficiencies and possible long-term moves towards a lower carbon electrified rail network.
A report published by the Institution of Mechanical Engineers in early 2009 states “as an option for the reduction of carbon emissions, the rail freight sector is leagues ahead of all the other options available. The target should therefore be to deliver far greater levels of growth in the rail-freight sector than are currently projected”
VALUE OF CARBON
Extrapolating values of carbon published in the Stern report and assuming an oil price of $80 a barrel, will drive a carbon value of £329 per tonne of carbon, which equates to a CO2 value of £89.73 tonne. If the forecast growth in rail freight can be achieved rail freight could be saving carbon worth at last £20.63 million by 2030 (if the oil price is higher than $80 a barrel then the value of carbon will also be higher).
FURTHER CARBON SAVINGSThe rail sector is also working hard to reduce its own carbon emissions. Widespread replacement of locomotives with newer, more fuel-efficient models, and increases in rail efficiencies has led to steady improvements over the last ten years, and further improvements are expected as longer, more efficient trains are operated.
Operators are using technology to reduce fuel consumption by monitoring and nurturing driver technique as well as reducing idling whilst trains are stopped and reducing the amount of light engine movements by for example investing in new fuelling points en route.
LONGER TRAINSEnabling longer freight trains will help to increase even further the carbon savings that can be achieved by modal shift. If more containers or bulk goods can be moved on each train then less
carbon per tonne of freight moved is produced.
Longer trains also make more efficient use of rail networks, as more freight can be moved in each timetabled pathway.
KEEPING FREIGHT TRAINS MOVINGJust like a car or a lorry, every time a freight train slows down or stops and then has to speed up again it uses more energy than if it can move at a constant speed. Investment in running loops and modified signalling could in the design of timetables to keep freight trains moving and reduce the carbon they produce. Every time a train is stopped it uses an average of 45 litres of additional fuel.
Great Lakes short-sea shipping gets boost: barge cargo service expands
McKeil Marine Ltd and Hunt’s Transport Ltd have more than doubled the capacity of their short-sea shipping service from the Port of Hamilton to Newfoundland after a successful trial run.
Hunt’s Transport leased the barge service, which is managed by Hamilton-based McKeil Marine, to transport cargo for its customers last summer after running into delays and capacity problems with the Marine Link ferry service to Newfoundland.
Last year, the barge service made four successful trips through the St. Lawrence Seaway to Argentia, Newfoundland. The service, which carries everything from construction materials and oversized equipment to general cargo on truck trailers, will now be expanded to nine trips this year.
Greer Hunt, president of Hunt’s Transport, said: “This is an operation we can move forward and add to our business model.That’s the route we’re barging ahead with. Much of the cargo is heading for mining and offshore projects. Atlantic Canada is having a bit of a boom and we’re looking at ways to take advantage of that.”
Hunt added that the capacity and fuel efficiency of barge transport provided significant environmental benefits. Normally, this cargo would be trucked all the way to North Sydney, Nova Scotia before being loaded onto the ferry to Newfoundland.
He said:“We can get 50 trailers onto a barge. Instead of 50 trucks burning fuel and releasing emissions into the atmosphere, we’ve got one barge with a much smaller carbon footprint.”
The first shipment of 2011 left Hamilton mid-April on the Niagara Spirit pushed by the tug John Spence. Subsequent trips, including one that left at the end of May carrying building materials, cranes and mobile homes, used the barge Lambert Spirit and tug Salvor.
Steve Fletcher, president of McKeil Marine, said: “We enjoy the challenge and we are happy to be working with Hunt’s Transport. If the demand grows we will look into the feasibility
of expanding the service, for now we will continue to offer a sound innovative solution to our customer.”
McKeil Marine and Hunt’s Transport have also recently formed a joint venture company to explore other areas of opportunity. This could involve services to more remote areas of Newfoundland and Labrador to deliver supplies and materials to specific industrial or construction projects.
Bruce Hodgson, market development director for the St. Lawrence Seaway Management Corporation, said that the Hunt-McKeil barge service was a good example of how short-sea shipping can be expanded in the Great Lakes-Seaway system.“It just shows there are market segments that can be serviced very well by short sea shipping in the Great Lakes. We need operators like McKeil, who are prepared to explore these opportunities. We compliment them on their innovative approach.”
ABOUT MCKEIL MARINE LTD
Family owned since 1956, McKeil Marine has a proud tradition with over half a century of service in the maritime sector on the Great Lakes and St. Lawrence Seaway. Headquartered in Hamilton and with an office in
Montreal, Quebec, its fleet of more than 40 tugs and barges carry general cargo, dry and liquid bulk, break bulk and project cargo to markets in Canada and the U.S.
ABOUT HUNT’S TRANSPORT LTDHunt’s Transport Ltd (HTL) is a transportation and logistics service provider led by founder and president, Greer Hunt, a businessman and entrepreneur in NL since the early 1980s.
Serving the demands of the oil, gas, mining, drilling, industrial, construction and general contracting industries, HTL provides truck, rail and marine transportation solutions. The company’s head office and warehouse is located in Mount Pearl, Newfoundland with a branch and 60,000ft2 warehouse facility in Cambridge, Ontario.
VIGAN barge unloading technology helps keep trucks off the roads
One 75-metre barge can transport the same amount of dry bulk as 60 trucks on 850 metres.
Inland transportation is of increasing interest against traffic jams — this a major reason why many industries prefer barge transport: it is also globally speaking cheaper.
A barge unloader installed at the Port of Liverpool in the UK at its Brocklebank Dock rapeseed crushing facility in 2002 has resulted in 2,500 fewer trucks a year on UK roads.
The VIGAN pneumatic unloader, which can discharge a ship at a rate of 170tph (tonnes per hour), was purchased with the assistance of a Department or Transport Freight Facility Grant.
“By shipping up to 5,000 tonnes at a time by sea from other parts of Britain and mainland Europe, we are not only securing valuable supplies for the plant and extra traffic for the port, but we are also substantially reducing the number of truck movements across the country’s network,” said Cargill’s port superintendent Andrew Polter.
For many years VIGAN has been a major player in pneumatic barge unloaders mainly in Europe with many installations in Belgium, Holland, France and Germany.
As a ‘premie`re’ for cocoa beans in bulk,VIGAN supplied a barge unloader to Cargill facility in Zandaam. The relevant factor is that cocoa beans are a delicate product to handle but thanks to its up-to-date technology,VIGAN manages the technological challenge to the full satisfaction of the customer.
A major advantage of the pneumatic unloaders for barges and inland transportation is the capability of sucking down to the latest product particles on the hold floor.
This technology is environmentally friendly: there is no dust and low noise (nearby urban areas). VIGAN’s equipment follows all the recent international regulations in terms of protecting the environment.
In 2004,VIGAN delivered also a barge unloader in China with a capacity of 400tph (near Chongqing along the Yangsi river). In 2005, two barge unloaders (each also with 400tph capacity) were delivered in Brazil for Cargill new facilities in Santarem along the Amazon river.
Another very interesting project was for the Cargill group in the Ukraine: unloading rail wagons and loading barges.
The fact that one of the most important company in the agri- business like Cargill is choosing pneumatic systems in several countries (Holland, Brazil, Ukraine and France) is a clear indication that they fully trust this technology as being the most suitable solution for this kind of barge unloading operations.
VIGAN has sold several barge unloaders to this company: two in Holland, one in France, one in England, one in Brazil and one in the Ukraine.
VIGAN has also sold two barge unloaders to the international group CERESTAR: one for Holland, and one for Germany.
The Soufflet group and Heineken are also purchasers of VIGAN’s barge unloading equipment.
For many years VIGAN has sold equipment for barge
unloading. The company is continuously making technological improvements to its equipment to increase reliability and reduce running costs.
The main advantages for barge unloading with a VIGAN pneumatic equipment are:
- the ability of the pneumatic systems to suck down to the latest particles of the cargo (also in hard-to-reach corners of the hold);
- low manpower: a one single operator is able to take care of the whole unloading operation;
- no dust or spillage; and
- low noise.
- low energy consumption (down to 0.6 kW per unloaded ton) thanks to most state-of-the art engineering and latest energy saving devices.
Most recently VIGAN has sold equipment for barge unloading in Belgium (one for grains in 2005 and another for urea in 2008).
Currently, a barge unloader with a capacity of 400tph is under manufacture at VIGAN’s facilities and will be delivered by the end of 2011 to the port of Se`te in France. This will ease the arrival of grains from the hinterland of France for onward transportation on large size vessels mainly to the African and Middle East markets.
Ingram Barge Company leads the way in environmental stewardship
Ingram Barge Company has been a quality marine transporter on America’s inland waterways since 1946, and has grown to become a pre-eminent carrier on America’s inland waterways. Ingram owns nearly 4,000 barges; those barges are powered by the industry’s best towboat fleet, which includes more than 130 towboats that are maintained at the highest level of standards. They transport a high volume of dry bulk commodities, including coal, aggregates, grain, fertilizer, ores, alloys, and steel products, as well as liquid bulk cargoes on over 4,500 miles of America’s inland waterways system. Since the middle of 2010, export coal volumes have increased steadily with shippers willing to enter multi-year transportation commitments to the US Gulf as a reliable and diversified outlet of coal from the US to the world market.
Remaining an industry leader in environmental stewardship is a commitment Ingram Barge Company takes seriously. The company recognizes that in the coming decades, business will be conducted in a world with greater transparency, higher energy and water costs, and increasingly strained natural resources. Ingram is devoted to being part of the solution, through modal efficiency, and actively pursuing methods to reduce consumption of natural resources throughout business operations. For its customers, this means moving more cargo over greater distances, using less energy and water and creating less waste.
Ingram feels its responsibility as the largest carrier on the inland waterway system is to lead in environmental sustainability. One example of its leadership in sustainability is the EPA SmartWay Program — In February 2010, Ingram Barge Company was named as one of the first marine transportation companies to be accepted as a partner in the US Environmental Protection Agency’s SmartWay Program. The programme requires measuring the environmental performance of a fleet, identifying goals for improving environmental performance within three years, submitting an action plan to the EPA within six months of agreement to participate, and reporting progress to the EPA annually.
CEO Craig Philip is very pleased with the progress the company is making towards becoming known for its sustainable practice. “It gives me great pleasure and pride to know that Ingram has been recognized and accepted into the EPA’s SmartWay Program as one of the first marine transportation companies,” Philip said. “Ingram is proud to be on the cutting edge of developing new policies and procedures for marine transportation companies as they relate to the environmental
issues at hand. Barge transport is already the greenest mode of bulk freight transport, and we will continue to do all that we can to take care of our environment and our associates.”
In addition, Ingram has partnered with several other agencies committed to the environment, such as The Nature Conservancy and the Mississippi River Corridor.
Through its partnership with the Mississippi River Corridor- Tennessee (MRCT), Ingram participated in an air emissions reduction programme for towboats operating on the Mississippi River by retrofitting six towboats in its industry-leading inland marine fleet with a unique diesel oxidation catalyst (DOC) unit and closed crank case emission control system.
Results of the programme included significant reductions in particulates, carbon monoxide, and hydrocarbons from exhaust emissions from the retrofitted vessels. Emissions testing has shown that the new DOC systems exhibited average particulate matter reductions of more than 40% and carbon monoxide and hydrocarbon reductions of more than 60%.
Through a partnership with The Nature Conservancy, a leading conservation organization that works around the world to protect ecologically important lands and waters, Ingram has made a financial commitment to support conservation efforts on lands located where Obion Creek and Bayou Du Chien flow into the Mississippi River in Fulton County, Kentucky. The Nature Conservancy will create a platform project with the potential to restore and reconnect over 18,000 acres of bottomland hardwood forests and wetlands to the Mississippi River alluvial floodplain within the next five years.
Ingram strives to set the standard and demonstrate new ways to further reduce the pollution associated with river transportation, which is already the most environmentally friendly mode of bulk freight transportation, as well as contribute to the restoration of the waterways on which it lives and serves. Ingram Barge Company is committed to continuous improvement, and strives to offer the best possible service and value for the transportation dollar.
Freightliner Group powers into new markets
One of the true success stories of privatization of the railways within the UK, Freightliner Group has established itself as the major player within the rail freight industry, in the UK and now additionally in Poland and Australia.
Ten times IFW Rail Freight Operator of the year, Freightliner Group is a dynamic and successful logistics company with a modern fleet of locomotives and rolling stock. Freightliner Group’s trains cover the entire UK rail network running over 1800 trains a week.
Freightliner’s operations in the UK intermodal market date back to 1965. Freightliner Group’s largest subsidiary, Freightliner Limited is the leading haulier of maritime containers in the UK and handles over 80% of all rail borne containers that enter the country.
Operating from the five key deep-sea ports Freightliner offers more than 100 daily services to and from 15 strategically located inland terminals. The opening of Bristol Railport in June 2010 increases the number of terminals owned by Freightliner to nine.
In 1999 Freightliner expanded the services it offered into bulk rail freight and formed a new subsidiary Freightliner Heavy Haul (FHH).
In operation for 12 years, FHH continues to provide excellent customer service and win new contracts as it builds its reputation for reliability, efficiency and innovative customer services. FHH is the leading provider of rail freight across a range of industries, operating services throughout the UK in the coal, aggregates, cement, specialist minerals and waste sectors. It also moves large numbers of trains in support of Network Rail’s own programme of track maintenance and renewals.
Earlier this year, FHH won its first contract to transport sand used for glass manufacture. The long-term partnership with Quinn Glass involves FHH providing the haulage and wagons as well as stock management of the sand from Sibelco UK Middleton Towers quarry near King’s Lynn to Quinn’s new state- of-the-art production plant at Elton, near Runcorn in Cheshire
The sand, used by Quinn Glass in the manufacture of glass containers for the food and beverage industries, is initially going into Quality Freight’s facility at Ellesmere Port and transferred by road. But, from November 2011, the Quinn Glass site will be
Freightliner’s first train for Quinn Glass.
rail-connected and the trains will go directly into a dedicated terminal and unloading facility there.
Adrian Curry, chief executive of Quinn Glass Ltd says: “We are very pleased to be partnering with Freightliner for our immediate rail and long-term rail freight haulage requirements and look forward to developing further opportunities in the months and years to come.”
As well as winning new contracts FHH services to the coal industry have also been recognized. In 2011 FHH was named Logistics Provider of the Year at the prestigious Coal UK
Awards, the third time in four years FHH has collected the award that is decided by a secret ballot among coal customers, producers, traders and supply chain partners
Martin Wilks, coal director and deputy managing director of Freightliner Heavy Haul Ltd, says:“We are delighted to be the recipients of this accolade, achieving recognition from customers and industry partners. It is rewarding recognition to all those at Freightliner whose dedication and hard work is key to providing our reliable, flexible and sustainable service. By working closely with our customers, mining companies and ports, we strive to play a key role at the heart of the industry. That role is one that we are proud to play.”
FHH uniquely, operates regularly into all the UK’s rail connected power stations and offers services from all the mines and coal ports that serve the energy market and in 2010 FHH celebrated carrying its 100 millionth tonne of coal.
FHH’s reputation for innovation is demonstrated by the introduction of the industry-leading PowerHaul locomotives.
The locomotives, a joint project between Freightliner and GE Transportation, have higher haulage and acceleration capabilities, increasing payloads per train and retaining timing criteria to
preserve rail network capacity, whilst lowering carbon emissions — bringing increased performance levels to FHH’s already competitive offering.
The locomotives have won a series of awards for innovation in the freight industry including the Freight Achievement of the Year at the 2010 National Rail Awards, the Technical Development award at the Rail Freight Group and IFW’s Technological Innovation award.
PowerHaul enables longer, heavier trains to be run in existing paths and new paths to be utilized that cut journey times and route mileages. PowerHaul’s ability to tackle a steep gradient on the route from Avonmouth to Rugely power station has decreased the journey by 60 miles in comparison to other UK locomotives thus producing fewer carbon emissions.
Since 1999, FHH has grown to a turnover of £100m, with over 600 employees, and a fleet of 80 locomotives and 1,300 wagons — a capital investment of more than £180m.
Using these resources, FHH has secured a position carrying approximately 40% of the bulk rail freight market in the UK.
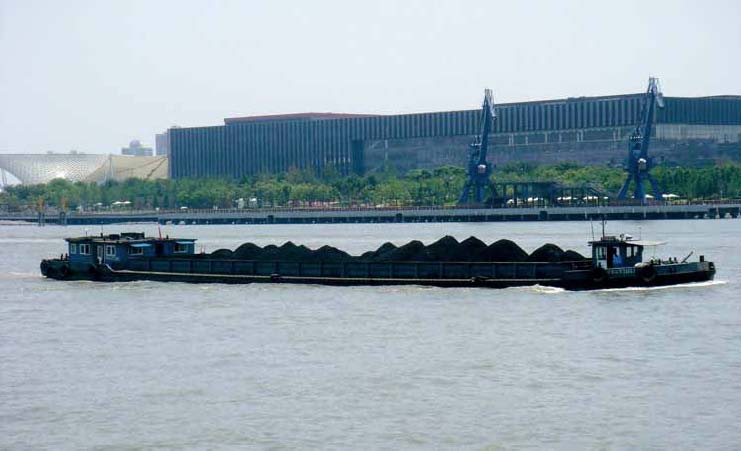
As well as operating carrier services, Freightliner also offers
maintenance solutions through its subsidiary Freightliner Maintenance Limited. Offering a nationwide service, bringing a fresh approach to the repair and maintenance of traction and rolling stock as well as infrastructure and maintenance solutions.
INTERNATIONAL OPERATIONS
Adapting the successful business models seen in the UK, Freightliner Group continues to develop into bulk rail freight sectors across Europe and Australia with the group’s two newest subsidiaries.
Freightliner Poland (FPL), which started operations in 2007, has seen great developments since signing its first three-month coal contract with Kozienice Power Station.
FPL now has multi-year deals within the coal, aggregates and petroleum industries for a variety of customers, employing over 150 personnel and operating a fleet of 19 locomotives and more than 900 wagons.
In less than five years, the company has developed into a dynamic rail freight company with
a reach throughout Poland and across borders into Germany and Ukraine.
Freightliner Australia Pty Ltd’s first contract was transporting containerized cotton from Wee Waa to Port Botany on behalf of Namoi Cotton.
It has since won a ten-year contract with Xstrata Coal for the provision of rail haulage services from its Hunter Valley coal mines in New South Wales to the port of Newcastle. The operation began in late 2010 with three train sets, each consisting of three locomotives and 90 wagons, and they are expected to provide haulage for about 10 million tonnes of coal a year.
Soaring costs make road and rail more efficient option for Brazilian operators
The need to cut costs, at a time when demand for farm commodities and minerals is soaring, means Brazil is increasingly turning to rail and inland waterway in preference to road, writes Patrick Knight.
Spurred by the increase in world population and rising living standards, demand for the grains, oilseeds and sugar produced in Brazil is accelerating, while demand for iron ore, bauxite and pulp is surging as well.
To keep pace and to reduce the cost of transport at time when the countries currency is strong, prejudicing competitiveness, Brazil has embarked on a major railway building programme. The first steps are also being taken to open up more of its 40,000km of navigable waterways to traffic. Only 8% of goods are now carried on inland waterways.
Work on three new railways, each about 1,700km long, is now under way. When they are complete and many other shorter lengths of track duplicated or upgraded, about 10,000km of new track will have been laid, taking the total to almost 40,000km. Thousands of new rail wagons, and hundreds of new locomotives are on order, a 500,000-tonnes-a-year plant to make rails may be added at a steel mill.
The percentage of goods carried by rail is expected to rise from the present 25% to at least 32%. Only 17% of goods went by rail before the system was privatized in 1997.
Three quarters of the 420mt (million tonnes) carried by rail last year was iron ore, and ore exports are expected to double to more than 600mt by 2020.
But as huge swathes of land are planted with extra soya, maize, cotton and sugar cane, as well as to commercial forests for making pulp and for industrial uses, the dominance of iron ore will gradually fall.
Increasing quantities of steel, the coal and coke needed to make it and the fertilizer needed on farms all over the country, most carried by rail, will be made.
Many of the 200 million hectares now used to graze cattle in the west, north and north east of the country, is being planted to soya, as land prices rise. So output is expected to increase from the record 72mt harvested this year, 47mt of it to be exported, to more than 100mt in seven or eight years time. Most of the extra will be exported.
A total of 35mt of maize, most fed to chickens and swine, is now produced in Brazil each year. But up to 8mt is exported in a good year, so output will also increase fast if world maize prices remain high.
The move north and west by soya explains why it makes sense to take more oilseeds by barge to the Amazon river along many of its tributaries. Building locks along half a dozen rivers and dredging others, will facilitate this.
One of the largest locks in the world, next to the Tucurui power plant on the Tocantins river in Amazonia, was opened to traffic last year.
Two 200 metres long locks, each with a 33-metre fall, will allow 20,000 tonnes barge trains to rise or fall in two stages.
The new lock opens 700km of river to barge traffic and will allow more of the soya, maize and cotton grown in Tocantins and Goias states to be taken cheaply to the port of Vila do Conde, on the main Amazon river, where bauxite is now made into alumina.
About 3mt of soya beans and meal already travels 1,100km down the Madeira river from Porto Velho, capital of Rondonia state, to the river port of Itacoatiara, on the main Amazon each
year, where it is transferred from barges to ocean going ships. This cuts the cost of getting soya from fields in the centre west to customers in Asia or Europe by at least 10%, compared with when Santos is used.
The Madeira river, which carries millions of tonnes of silt down from the Andes mountains each year, will be dredged to allow up to 20mt of soya to reach Itacoatiara port at a fraction of the cost needed to truck it 2,000km to Santos.
Key to the rail expansion programme is the completion of the 2,100km-long North–South line. North–South tracks link with the Vale companies 890km Carajas line, which now takes 100mt of ore from the Carajas mines to the deep water port of Itaqui, in Maranhao state, each year.
About 700km of North–South track have already been laid and is used to carry soya and maize, as well as wood and pig iron to the coast. Fertilizer is a leading return cargo. The North–South line should be completed by the end of this year, allowing much more than the present 2mt of soya to leave from Itaqui each year.
At least 10% more iron ore is now exported each year, mainly because of the almost insatiable demand from China, now Brazil’s leading customer for the product.
To cope, the Carajas railway is being duplicated along the whole of its 890km length, while a 100km extension will give access to a completely new complex being opened up. The line will soon be carrying 200mt of ore each year to Itaqui.
Brazil is far from its leading customers Asia, destination of 65% of Brazil’s ore. Customers include not only China, but Japan, Taiwan, South Korea and the Philippines as well. To be able to compete with ore from Australia and India means transport costs must be reduced. Which is why new railway lines, as well as much larger ships are being built.
Trains carrying ore from Carajas to Itaqui are more than 4km long, with 330 wagons being hauled by three locomotives. Each train carries 40,000 tonnes of ore, so two trains can fill all but the largest vessels.
Two brand new lines are now being built to link ports on the Atlantic coast to the North–South line, passing through regions where soya is grown on the way. The furthest advanced is the 1,700km ‘Transnordestina’ line, which will link the ports of Pecem in Ceara state and Suape in Pernambuco with the North- South line.This will allow up to 20mt of soya, as well as other crops, to reach the Atlantic faster and more cheaply than now.
Five-hundred kilometres further south, the East-West line will link the port of Ilheus, from which 2mt of soya beans and meal were shipped last year, to the North-South line. The new line will pass through the soya producing area of Bahia state, where about 3mt of soya are now grown, to link with the North-South line in Goias state, where 7.5mt of soya is produced each year.
At the moment, most of the 320mt of iron ore which Brazil exports each year is taken to ports either along the Carajas line, along the 700km ‘Vitoria-Minas’ line, which takes ore produced in Minas Gerais to the port of Tubarao, or the 600km ‘Steel Line’ which takes ore to the Guaiba/Sepetiba port complex in Rio de Janeiro state.
But large deposits of iron ore have been found in the state of Bahia, along with other non-ferrous metals and these will be taken to Ilheus along the East–West line, as will sugar to be produced at new mills.
Brazil now exports about 25mt of sugar each year, two-thirds of which leaves via Santos. Most of the other third uses Paranagua, in Parana state, although about 2mt leaves from Recife or Maceio in the north east of the country each year.
Last year, 7.5mt of sugar was taken to Santos by rail, much of
it produced by the Cosan company, now in partnership with the Shell oil company.
Cosan has ordered 800 new specialized wagons as well as 50 locomotives.
Improvements at Santos now allow trains of 80 wagons, rather than 40 previously, to reach warehouses which can store 800,000 tonnes, without any conflict with trucks. Until recently, all the sugar was taken to Santos by truck, but the greater use of rail means many fewer trucks are now needed.
Work will soon start on building a new link to by-pass Sao Paulo city, through which most trains must now pass. They can only use tracks between one and five in the morning because of heavy commuter traffic, which greatly limits the tonnage which can use this route.
Powerful new locomotives to take rail wagons down the ‘rack’ system which drops 700 metres down the escarpment to Santos have been bought, which will speed up traffic on this route. A 20km conveyor belt will soon be carrying iron ore to a steel mill in Santos, rather than it going by train.
A second line which reaches Santos, owned by the Latin American Logistics Company, ALL, which also owns many lines in Argentina, is to be upgraded.
The numerous tunnels on this route are to be deepened, allowing containers to be double stacked.
The Petrobras oil company has recently ordered 80 barges and the 20 vessels needed to push them, for use on the Tiete- Parana waterway system, which stretches 1,200km through Sao Paulo, Minas Gerais, Parana and Goias states.
This waterway is now used to carry soya beans, sugar cane and building materials, such as sand, as well as fertilizer. A 200km stretch is now being opened up, which will make it navigable to within 100km of Sao Paulo city.
AEP River Operations transports over 75mt of dry cargo each year
AEP River Operations is headquartered in St. Louis, Missouri. It is a barge company offering high-quality service in the transportation of dry bulk commodities throughout the inland river system. This includes the movement of grain, project cargo, coal, steel, ores and other bulk products.
AEP has been active in the river transportation business for nearly 40 years, and has earned a reputation for excellence. Its services include: y barge transportation and 24-hour on-call dispatch; y shipyard services; y barge cleaning and repair; y assistance in identifying the best combination of stevedores and terminals to meet its customers’ cost and quality objectives; and y project cargo logistics co-ordination.
Reducing operational ‘carbon footprints’ has become a major issue for companies around the globe. AEP River Operations is already working in a market that offers one of the ‘greenest’ ways of transporting bulk cargo, but it is not stopping there. The company is continually improving its environmental credentials by improving the efficiency of its water vessels, both to save money and reduce its environmental impacts. It has placed seven new towboats into service and repowered three boats with engines that meet Tier II air quality standards. The Tier II engines reduce fuel consumption by approximately 5% and particulate matter emissions by approximately 50%. These vessels not only improve performance, they also enhance crew comfort.
AEP River Operations has a recycling programme on its river vessels called SEE Green. In 2010, in its Gulf operations and vessel line boats estimates more than 84 tonnes of waste was recycled, ranging from cardboard boxes, plastic and miscellaneous lines, dramatically reducing landfill costs and associated environmental impacts. The company’s efforts continue to be industry-leading as its peers on the river have looked to AEP River Operations for guidance in kicking off their own recycling efforts. It expects to expand its own efforts in 2011.
Bulk commodities transported by AEP River Operations include: steel, grain fertilizer, cement, lime, limestone, project cargo, aluminium, gypsum, coal, petcoke, ores, steel raw materials, scrap metals, sand, and gravel.
The company has a total of 3,250 barges and 90 boats, and is working in a market where there are five or six fully integrated competitors.
One of the major strategic objectives of AEP River Operations is to provide for the safety, health and wellbeing of its employees. At the end of May 2011, its injury recordable rate was 0.76. Severity rate thru May 2011 was 11.83; loss is based on restricted work days. Thirty-four of AEP’s boats received the Devlin Award for working at least two years without a lost-time accident, and collectively, these boats have worked 156 years without a lost-time event. AEP’s Gulf group won the coveted Mariner’s Award for its overall safety leadership efforts.
Among recent developments at the company is the emergence of a new commodity (frac sand) that is a direct result of the increase in shale gas production in the regions of Texas, Pennsylvania and Oklahoma. There has also been a strong demand for export coal.
AEP River Operations is a wholly-owned subsidiary of American Electric Power (AEP). AEP is one of the largest electric utilities in the United States.
AEP River Operations is a fully integrated barge line delivering over 75mt (million tonnes) of dry cargo each year. Its fleet of boats and barges operates along the Gulf Coast to as far north as Minneapolis, Chicago, and Pittsburgh and to as far south and west as Brownsville and Catoosa and points in between. The company’s headquarters is in St. Louis, Missouri with regional operations in Pittsburgh, New Orleans, and Mobile. AEP River Operations’ boat and barge operations are in Lakin,WV and Paducah, KY with Gulf operations including a full-service shipyard, barge cleaning and repair, fleeting and shifting, and midstream transfers.