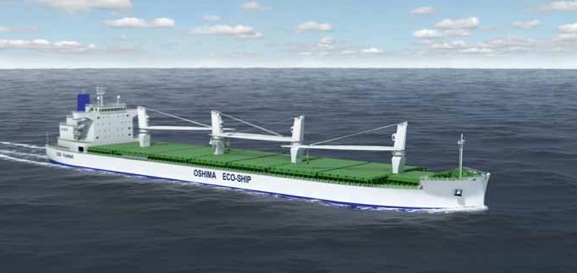
Historically low freight rates are increasing the pressure on vessel operators to reduce costs. This is creating new safety risks but also pushing ship design parameters and encouraging innovation, writes Michael King.
In a low freight environment it is not surprising that owners are seeking commercial advantage where they can find it. What is unusual is that one of the tactics being deployed to achieve this is the ordering of new ships, adding capacity to a market already devastated by an excess of vessels.
Owners with big pockets or access to capital markets are buying new ships for a number of reasons. Some are seeking a competitive advantage by reducing their fuel costs through the deployment of more efficient ‘eco’ designs. These designs typically incorporate more efficient hull lines, and machinery and propulsion systems that slash fuel requirements and help meet more stringent emissions regulations.
For other buyers the economies of scale generated by deploying larger ships and/or locking in forward freight costs is a strong ‘pull’.
Both trends are only possible, of course, due to the record low newbuilding prices available at yards in China and elsewhere which are tempting owners even in a depressed market.
“ECO ships are more economical to operate,” said Nick Brown, marine communications manager at Lloyd’s Register. “No owner is going to a yard saying they would like to order designs from a few years ago. They are simply the ships available today. We expect to see demand for further economies continuing.”
The change is forcing classification societies to focus less on traditional areas of expertise such as hull and mechanical certification and become more involved in verification in the areas of operational and environmental performance, according to Howard Fireman, vice president of Operational and Environmental Performance at ABS.
“From a technology perspective, we see that the industry is now going through a period of significant but incremental change principally driven by increasing fuel costs and regulations,” he said. “This is witnessed by new ships having progressively cleaner air emissions and higher energy efficiency, which impacts future commercial decisions.
“In the long term, this will require class societies to identify risk-based, more efficient, less intrusive, technology-driven and monitoring-based processes.”
DNV is currently working on a number of major new bulk carrier designs which incorporate the latest ‘ECO’ technology. “We believe that it is likely that the era of cheap fuel is over in the short to medium term,” said DNV Bulk Carrier Segment Director Michael Aasland. “Fuel efficiency is therefore here to stay, both in order to reduce costs of operation but also in order to make shipping an even more environmentally friendly mode of transport.”
The common theme across DNV’s new concept designs is the constant desire to reduce fuel consumption. This is achieved through the optimization of hull lines through extensive use of Computation Fluid Dynamic tools, and use of the latest engine technology and fuel efficiency devices.
‘Oshima ECO-Ship 2020’, for example, is an Open Hatch Bulk Carrier developed as a joint project by DNV and Oshima Shipbuilding and designed to emit 60% less CO2 than standard designs. It features a wide twin skeg hull fitted with Oshima’s ‘Seaworthy’ bow and air lubrication system, a waste heat recovery system and a twin screw redundant propulsion system.
It also boasts an LNG single-fuel solution designed with Rolls Royce and a lean-burn 4-stroke medium speed natural gas engine.
The idea behind the design and the use of LNG is to ‘forward proof’ vessels against more stringent environmental regulations expected to be introduced by 2020, not least those restricting heavy fuel usage in Emission Control Areas. Because LNG contains no sulphur and the LNG combustion process emits 90% less NOx and eliminates almost all particulate emissions, DNV concluded this was the most efficient fuel. Moreover, DNV takes the view that cost of the system — expensive at present — is likely to fall significantly in the future.
The ship’s design also assumes that slow steaming strategies are here to stay because fuel prices will remain high. The ‘Oshima’ has a design speed of just 14.5 knots to aid the reduction of fuel consumption. “Reduced design speed allows for a wide hull form and a twin screw propulsion system with high propulsive efficiency,” said Aasland. “High propulsive efficiency along with low hull resistance and fuel consumption are the main features of the design.”
However, while slowing ships down and using innovative fuel and fuel systems can help improve efficiency, a number of those contacted for this article by DCI expressed apprehension about some of the latest ECO ship designs, not least due to the potential danger posed by under-powered vessels. “There is a concern that lower engine power may result in safety issues if this is taken to extremes,” admits Aasland.
Fireman said ABS was now working with IACS and other industry partners to finalize IMO recommendations for minimum powering. “This is intended to address the concern that decreases in fuel consumption can be achieved through the use of under-sized main engines,” he added.
Classification societies also have mixed views on whether bulk carriers will continue to get larger. The attraction of bigger ships is easy to pinpoint:“Large ships have an advantage from an economy of scale point of view, which is not unimportant in these times of high fuel prices,” said Aasland.
Vale’s fleet of ‘Valemax’ very large ore carriers (VLOC) designed to carry ore from Brazil are up to 400,000dwt in size and have changed the dynamics of the iron ore trade.
“The Valemaxes are very special ships and they were ordered by Vale in order to render the company’s iron ore exports to China more competitive compared to Australian exports,” said Konstantinos Chatzitolios, Manager for Bulk Carriers at Bureau Veritas. “This is the case usually for very big ships which are built for a specific job in mind. Their success depends on the success of this job. In the case of the Valemaxes, their competitive advantage was lost the moment they set to seas due to their ban from Chinese ports.”
Chatzitolios thinks it is unlikely more orders for VLOCs will be placed even though newbuilding prices have flat-lined in the past few months, at least until they are admitted to berth with full cargo holds at Chinese ports.
But he warns those that are tempted by low prices to understand that structural stresses and dangers increase in line with the size of the ship. “The hull girder loads increase with size and also the ship becomes more prone to hydro-elastic phenomena like whipping and springing at ultra large dimensions,” he said. “If whipping is not taken into consideration when designing ultra large ships, which can become very elastic, then there is a risk of catastrophic failure and hull girder collapse from extreme slamming loads.
“Springing on the other hand adds significant fatigue damage to certain details of the ship which are already prone to fatigue like hatch corners. Proper software tools and clear methodology are needed to examine accurately the hydro elastic effects on large vessels.”
To this end, BV has developed a comprehensive methodology and advanced HOMER software in order to assess the hydro-elastic effects of whipping and springing on big ships. “Our calculations on recent ore carriers show that the additional stresses due to the ship’s elasticity are not negligible and for this size of ship the traditional rigid approach is not sufficient,” he said.
BV is currently studying the latest iron ore carrier designs and their ability to withstand the loads imposed by fast loading rates.The society is also offering ship owners the opportunity to have their ships examined for use with high speed single-pour loading techniques which can reduce considerably the time spent at ports. Those that pass the exam can earn the additional class notation — SINGLEPASSLOADING.
“Heavy cargoes, grab loading and fast loading rates paint the picture of a very demanding service life,” said Chatzitolios. “Alternate loading conditions with heavy cargoes increase the hull girder loads. Fast loading rates of heavy cargo, which is a usual practice in many ports, can damage the ship with sometimes severe results. Most of the times this is due to local strength problems and the inability of the ballast pumps to de- ballast the ship compared to the faster shiploaders.”
Dino Cervetto, Head of Technical Services at RINA Services, believes the technology is already available to build bigger bulkers safely, although he admits the market does not need these vessels at present.
“Perhaps there will be demand for more if and when Vale is able to berth their ships in China,” he told DCI. “If that does happen, then the big issue is to be sure what the loads on the structure are. Each new design will need a sea keeping load analysis associated with spectral fatigue analyses to get that right, and a full structural analysis. It is a lot of work but it can be done and the tools we have are really reliable to support a skilled and experienced engineering judgement of the results.”
He also raised the issue of loading rates and the stresses these are placing on bulk carrier structures. “Ports are loading faster and faster and we as class cannot control or even influence that,” he said. “We see two main issues, local impact on the structure and the capacity of the ballast system to cope with the loading speeds and also maintain stresses within the loading conditions.”